Kenworth Truck Co. recently celebrated its 100th anniversary. The company has been a pillar of manufacturing activity in the Seattle area since 1923, operating out of a series of four different local factories, including its current flagship plant in Renton, which has been in operation for 31 years. While the Class 7 and Class 8 vehicles rolling off the state-of-the-art assembly line have evolved over the years, they’re still renowned for dependability, durability and quality.
That’s because Kenworth, a division of PACCAR Inc., continuously applies the latest production technology to improve the way it assembles custom-engineered, build-to-order trucks. The company has developed and implemented a variety of high-tech tools and systems on the plant floor to assemble products better, faster and more efficiently than its competitors.
The Renton plant continues to build the widest breadth of Kenworth models used in a variety of applications, including aerodynamic long-haul vehicles such as the T680, versatile workhorse trucks like the T800 and T880, and the burly W900, which graced the cover of ASSEMBLY magazine in November 2004. The factory also continues to make the C500, a rugged off-road model that can be found hard at work in oil fields, mines, logging camps, construction sites and other remote locations around the world.
However, one big change over the last two decades has been the creation of a proprietary power train. Today, PACCAR MX-11 and MX-13 diesel engines are offered in most Kenworth models built at Renton.
But, the new kid in Kenworth’s legendary lineup of heavy-duty trucks is the T680E. The battery-powered Class 8 vehicle features a 396-kilowatt-hour battery and an average operating range of 150 miles, depending on the application.
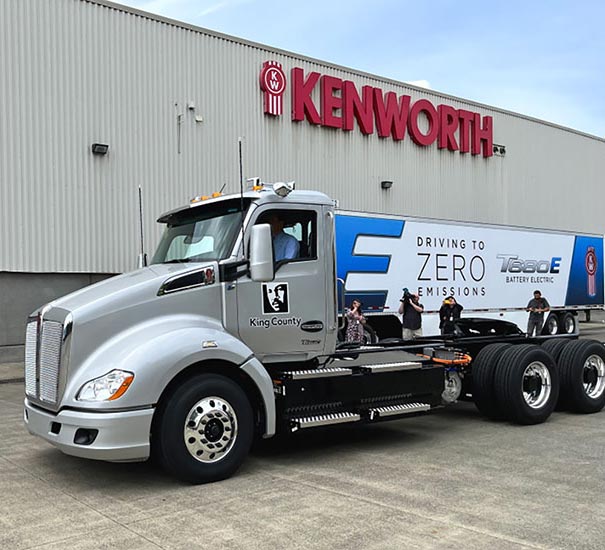
The T680E electric truck is made on the same assembly line as Kenworth’s traditional diesel-powered models. Photo courtesy Kenworth Truck Co.
“Proximity to [our corporate] headquarters, R&D center and PACCAR’s technology center, makes the Renton location well suited to support the development of new alternate fuel power trains with early validation builds,” says Scott Smith, plant manager.
“Building the T680E alongside our other models required production adjustments, such as building the nonpowered unit online while installing the BEV power train offline,” explains Smith. “It runs down the main assembly line as our diesel-powered trucks. [However], the T680E has batteries in place of fuel tanks and a power control accessory unit in place of a diesel engine.”
When it received the inaugural Assembly Plant of the Year award in 2004, the facility excelled at lean production. Kenworth engineers applied Six Sigma methodology to production processes, quality control, new product introductions and transactional processes.
“[Today], Renton continues to be a leader in technology and innovation through our application of Six Sigma methodology and introduction of lean manufacturing principles guided by the PACCAR Production System,” says Smith. “Our leadership team and lean practitioners have onsite resources who teach and coach lean skills at the operator level.
“The assembly line configuration is also similar to the way it was in 2004, except for integration of the C500 off-highway truck,” notes Smith. “The C500 model was a stall-build configuration. But, through the application of Six Sigma and lean, we now produce it on the main assembly line with the other models. Implementing modifications from learnings such as these allow us to absorb wide product fluctuations into our unique mixed-model build process, providing flexibility to incorporate the production of new models on the line."
The Renton plant continues to invest in and standardize technologies that improve productivity, quality and drive zero unplanned downtime of mission-critical machines and processes.
“Six Sigma methodology is used to make data-driven decisions and to validate our improvements,” Smith points out. “Kenworth has a culture of continuous improvement where all employees participate in utilizing a seven-step process to identify short- and long-term actions. We believe small improvements add up over time.

This new assembly tool provides a significant time savings for headlamp installation. Photo courtesy Kenworth Truck Co.
“Through technological advancements in tooling, such as moving from air-over-hydraulic impact wrenches to DC electric tools that produce a better torqued joint, we have reduced employee noise exposure and ergonomic issue risks,” explains Smith. “To improve process capability, we have introduced automated fluid fill for the specific quantities required by each chassis, as well as electrostatic paint.
“Striking a balance between operational efficiency and sustainable operations is a priority in Renton,” claims Smith. “For example, advancements in paint technology systems that communicate with the mix machines ensure paint quantity is exactly matched to what is being painted.
“We offer every color offered by our paint supplier,” Smith points out. “With more than 20,000 colors for customers to choose from, this level of specificity ensures efficiency while cutting down on waste and reducing emissions. Renton is known to have some of the lowest paint usage per vehicle across PACCAR manufacturing and this is achieved through upgraded technology in robotics with electrostatics.
“PACCAR developed a North American materials organization that accelerated our benchmarking and adoption of best practices,” adds Smith. “For us to produce highly complex, custom-ordered vehicles with a wide variety of parts on the same assembly line with the same workforce, we implemented chassis-specific kitting at each build station.

Kenworth uses DC electric fastening tools to monitor torque and ensure quality. Photo courtesy Kenworth Truck Co.
“The kits need to be highly accurate in part selection and we use pick-to-voice and pick-to-light technologies to ensure accuracy,” notes Smith. "[They ensure] just-in-time delivery of parts to the assembly line, plus elimination of inventory and warehousing space, allowing the plant to be focused on product assembly.”
The Renton factory has also experimented with augmented reality devices as a training tool and has introduced new technologies for monitoring equipment and systems, such as the implementation of machine health optimization sensors, PLC data and RFID tracing.
“Equipment is now monitored for potential failure using sensors to detect temperature and vibration,” says Smith. “Through analysis, the system can predict problems before they occur, which eliminates unplanned downtime and ultimately prevents catastrophic failure. We also monitor PLC data [using an integrated software platform] and have implemented RFID tags for tracking critical assets.”
Kenworth Renton uses online dashboards to deliver critical, area-specific, key process indicators to employees in real time. That ensures that safety, quality, productivity and timely resolution of assembly issues are achieved. The right information, provided at the right time, in the right way, to the right individual is the driving theme.

The T680 is one of the most popular trucks produced at Kenworth’s state-of-the-art factory in Renton, WA. It is available in several different configurations, including (left to right) a day cab, a 52-inch sleeper and a 76-inch sleeper. Photo courtesy Kenworth Truck Co.
“To expedite tooling, assembly aides and prototyping, we also utilize in-house 3D printing to make custom assembly fixtures that help with quality and ergonomics,” says Smith.
The Renton factory has been recognized by the National Association of Manufacturers for several plant floor initiatives. One recent example that received a Manufacturing Leadership Award was the sealed beam headlamp aimer project. Working with engineering students at Washington State University, the plant’s project team developed custom tooling to enhance efficiency for the installation of headlamps in legacy models. Kenworth engineers used additive manufacturing technology during final design processes to make replacement parts for the new tools both cost effective and readily available.
Kenworth Renton and its sister plant in plant in Chillicothe, OH, have both earned ISO 14001:2015 certification for effective environmental management systems established to help build Class 8 trucks in a sustainable manner. “Renton is raising the bar by continuing to reduce its carbon footprint through energy management,” says Smith. “A new system that monitors energy usage by area in real time has been implemented to measure where power and natural gas is being used and the pattern of usage.
“These patterns lead to unexpected energy management opportunities that would not have been known without the data collection and analysis tools,” claims Smith. “Renton was selected as the first proof of concept for this system and the improvements achieved will eventually become a PACCAR-wide initiative.”
Click here to learn more about the Assembly Plant of the Year award or to nominate a facility for 2024 (the deadline is May 1).