Schneider Electric’s facility in Lexington, KY, holds the distinction of being named both the Assembly Plant of the Year and a Lighthouse factory. The 500,000-square-foot plant has been mass-producing load centers and safety switches since Dwight D. Eisenhower was president. It opened in 1957, a year before the first issue of ASSEMBLY magazine rolled off the printing press.
Since then, the low-mix, high-volume assembly plant has not rested on its laurels. It has thrived on continuous improvement and has become a state-of-the-art showcase for digital manufacturing. Today, Schneider Electric Lexington is one of the most advanced factories in the United States.
The brownfield facility is a leader in applying Industry 4.0 tools that empower operators, reduce costs and improve productivity. In fact, the plant is recognized by the World Economic Forum as both an Advanced Lighthouse and a Sustainability Lighthouse for its adoption and use of 4IR technologies, and for achieving sustainability and productivity breakthroughs, respectively.
Schneider Electric has invested millions of dollars in its Lexington plant, including installing new equipment and machinery with connected technology and automation. The new technology, coupled with using an architecture optimized for digitization, has helped increase the plants' quality and capacity and make its operations more energy efficient.
The upgrades enabled by digitization and connectivity have improved operational efficiency and mean time between failures. Because production equipment is connected, employees can monitor and adjust energy usage and perform a variety of diagnostic and predictive maintenance tasks.
Load centers are nondistinctive metal boxes that house an assortment of bus bars and other aluminum, copper and plastic components that distribute and control low-voltage electricity. Contractors and builders buy the boxes and electricians stuff them with different types of circuit breakers to protect apartments, condominiums and houses from electrical overloads and short circuits.
It’s a simple solution to a potentially deadly problem. Although most load centers look the same, they’re not. A wide variety of options are available. In fact, assemblers at the Lexington plant build more than 200 different configurations of load centers. And, safety switches vary in size from 30 to 200 amps.
To maintain high levels of quality and productivity, while keeping lead times and costs low, Schneider Electric Lexington is a vertically integrated facility. All metal stamping, plastic injection molding, electroplating and painting is done in-house, in addition to packaging. The plant also features state-of-the-art production equipment.

Schneider Electric Lexington has digitized the entire continuous improvement process. Photo courtesy Schneider Electric
“We have added more than 25 robots to improve material handling and to address ergonomic issues,” says Mike Labhart, director of innovation and smart factory at Schneider Electric. “We use them for machine tending applications. For instance, in the fabrication department, we use six-axis robots to pick up metal enclosures and place them on a hook attached to the conveyor system. Those repetitive tasks used to be done manually.
“We now produce an average of 10,000 load centers a day vs. 8,000 back in 2007,” notes Labhart. “Everything is assembled with DC electric drivers equipped with torque monitoring for critical joints.
“The overall footprint of the products we make is the same,” Labhart points out. “However, the complexity has increased slightly. We’ve seen several major product enhancements and feature changes, such as plug-on-neutral load centers.”
The biggest physical change to the Lexington plant over the last 17 years is a $4 million power-and-free conveyor system that has improved productivity and ergonomics by delivering painted parts directly to assembly workstations. The one-mile-long conveyor snaking through the plant has eliminated manual palletizing and greatly reduced internal fork truck traffic.
“Conveyors have enabled us to streamline material handling,” says Labhart. “The amount of work in process (WIP) has been significantly reduced to prevent blockages from the press department to welding and then from the paint shop to final assembly. RFID tags tied into a PLC enable us to track and synchronize WIP movement throughout the facility.
“The conveyor system has eliminated palletization and more than 120 miles a day of forklift movement,” claims Labhart. “At any given time, more than 7,000 parts are moving on the new system.
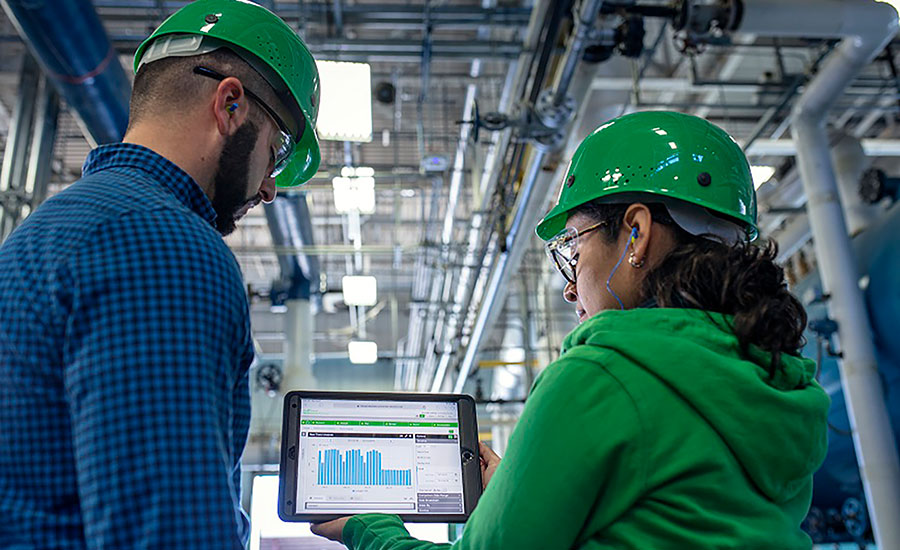
Upgrades enabled by digitization and connectivity have improved operational efficiency and mean time between failures. Photo courtesy Schneider Electric
“The conveyor enabled us to gain a 25 percent increase in production volume without having to change the physical size of the plant,” explains Labhart. “It also helped us free up a lot of space for new equipment.
“Our processes are complex and, as with any aged facility, there are multiple applications that have evolved from necessity,” adds Labhart. “Often, these legacy applications made data sharing and analysis difficult, as proprietary systems tend to silo valuable information. To drive higher levels of efficiency, we recognized that those data silos needed to be unlocked.”
The Lexington facility’s digital journey began about 15 years ago when connected products were deployed on the plant floor to eliminate material handling waste. At the time, an RFID system was installed and it eventually delivered more than $1 million in productivity gains.
This base of connected products enabled the factory to take the next steps: more precise edge control, plus a new generation of advanced software apps and data analytics.
In addition, the system has been completely integrated with an ERP system from SAP. It’s the heart of all functions in the plant. Manufacturing execution systems have been integrated with it so that the flow from order to assembly occurs seamlessly.

Because production equipment is connected, employees can monitor energy usage and perform a variety of diagnostic and predictive maintenance tasks. Photo courtesy Schneider Electric
The Lexington plant harnesses Schneider Electric’s Industrial Internet of Things (IIoT) based EcoStruxure system, which provides digital tools such as augmented reality, remote monitoring and predictive maintenance to drive energy efficiency, sustainability and overall cost savings.
“By making our existing infrastructure smarter, we are able to extract data that was never available to us because it was trapped in silos; we now use that data to make the right decisions quickly,” says Labhart. “We are quite developed at the connected products level. The push buttons, lights, back lights, terminal strips, limit switches, photo eyes, RFID switches and HMIs are all connected."
Today, the Lexington plant continues to drive efficiencies and establish new smart factory benchmarks. For instance, monitoring and analyzing energy usage has driven a large annual savings.
“Our smart factory program has developed standards for machine learning and IoT technology,” explains Labhart. “We have deployed platforms and infrastructure to support data streaming of critical signals from equipment, such as pressure, temperature and vibration. We currently have nearly 3,000 signals that are streaming from the factory floor. We use that data for visualization and to detect anomalies in production operations.
“We have also digitized the entire continuous improvement process,” Labhart points out. “Our lean digitization system has eliminated the use of boards and markers, which were commonly used to communicate back in 2007.
“It collects and calculates performance data, creates digital reports and delivers digital andon information to the factory floor that goes out through mobile devices,” says Labhart. “Another tool gives us the ability to manage the resources and the actions associated with continuous improvement.
“We’ve also adopted artificial intelligence technology for asset health,” adds Labhart. “The conveyor system uses a deep-learning platform to analyze components and detect any anomalies. In the future, we want to take our deep learning and advanced vision systems to the next level to further improve product quality and address asset health.
“Many things that were initially adopted and tested in Lexington, including our standard architecture for IoT and edge applications, are now shaping new facilities, such as our recently opened plant in El Paso, TX,” concludes Labhart.Click here to learn more about the Assembly Plant of the Year award or to nominate a facility for 2024 (the deadline is May 1).