During the past 20 years of the Assembly Plant of the Year award, only one company has received the honor twice. That’s Ford Motor Co. The automaker’s Michigan Assembly Plant in Wayne, MI, received the award in 2012, while its Van Dyke transmission plant in Sterling Heights, MI, won in 2018.
Both facilities have undergone major transformations since they received the award. That’s due to the evolving nature of the auto industry and changing consumer demand.
The Michigan Assembly Plant went from making small, fuel-efficient cars to sport utility vehicles and pickup trucks. Meanwhile, the Van Dyke plant was retooled to make motors and transaxles for electric vehicles. Each facility has withstood those major changes plus many other recent production disruptions, including Covid, supply chain shortages and the UAW strike.
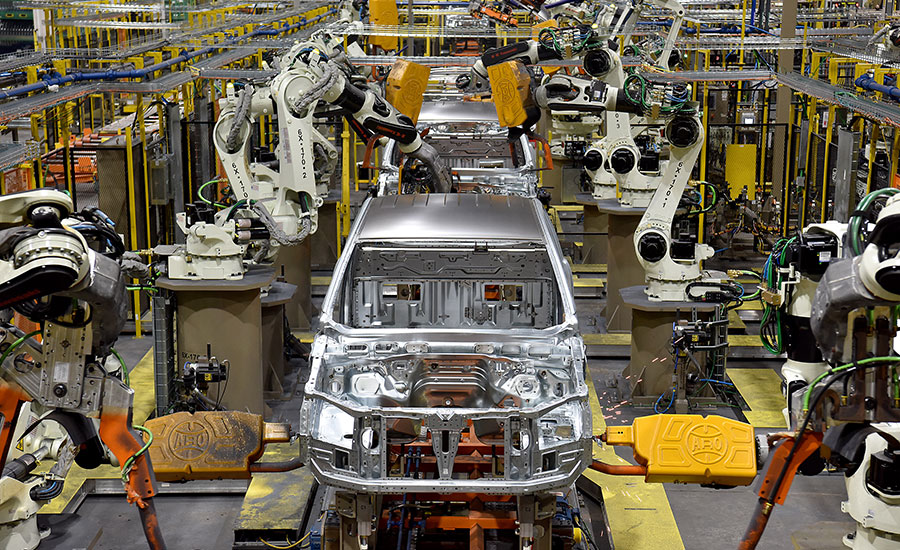
The Ranger pickup truck is also made at the Michigan Assembly Plant today. Photo courtesy Ford Motor Co.
The Michigan Assembly Plant is located a short drive west of Ford’s corporate headquarters. The factory is a consolidation of two facilities that were built in the boom years of the 1950s: Michigan Truck and Wayne Stamping and Assembly. The former was built in 1957 to produce station wagons.
The building was christened the Michigan Truck Plant in 1964 when it began assembling F-100 pickups. The factory also produced Broncos from 1966 to 1996. Michigan Assembly gained acclaim as being among the most important and profitable factories in the world when it made Ford Expeditions and Lincoln Navigators from 1996 to 2008.
By 2012, the facility had once again undergone multiple changes and was building four versions of the Focus compact sedan and two versions of the C-Max crossover. It served as a showcase for producing multiple power train models—gas, electric, hybrid and plug-in hybrid—on the same assembly line in environmentally friendly ways.
Ford engineers also pioneered new tools and technology in the plant, such as an upper body exoskeleton for performing repetitive tasks. Operators on overhead clamshell assembly lines used the device for awkward tasks such as attaching brake and fuel lines.
In 2017, Ford announced plans to invest $850 million in the Michigan Assembly Plant to build the all-new Bronco and Ranger. The company proclaimed it was “a renaissance for a plant just outside of Detroit that has experienced the highs and lows of the American auto industry for the past six decades.”

The Van Dyke transmission plant hung a large banner on the front of the facility in 2018 to celebrate being the Assembly Plant of the Year. Photo courtesy Ford Motor Co.
Ranger production began at the plant in 2018, followed by the Bronco in 2021. The massive retooling effort included a modification center that specializes in factory-installed extras such as front bumper safari bars, roof racks and exterior graphic packages.
Earlier this year, Ford announced plans to create nearly 900 jobs as part of a new third crew at the Michigan Assembly Plant to meet surging demand for various Bronco and Ranger models. The company said the initiative would enable it to move “nimbly across its global footprint to capitalize on its balanced lineup and serve customers with the right mix of gas-powered, hybrid and electric vehicles, while optimizing financial returns…The new 1,600-person third crew at Michigan Assembly Plant will also include approximately 700 employees from Ford’s Rouge Complex in Dearborn who applied for job openings.”
“[We are] adding the manpower this summer to support planned future volume increases for vehicle lines assembled at the plant,” says Jim Farley, president and CEO of Ford Motor Co. “The all-new Ranger and Ranger Raptor are on track to launch this year. Michigan Assembly Plant will transition to producing vehicles seven days a week vs. five currently, with three crews working two shifts…We are taking advantage of our manufacturing flexibility to offer customers choices while balancing our growth and profitability.”

Today, the Van Dyke Electric Powertrain Center assembles motors and transaxles used in battery-powered vehicles. Photo courtesy Ford Motor Co.
The Van Dyke plant, located in a northern suburb of Detroit, is named after a major thoroughfare. When it received the Assembly Plant of the Year in 2018, the facility was mass-producing 67 different transmission models for 24 North American Ford assembly plants and 13 overseas facilities.
Employees at the plant basked in the spotlight of receiving the award and proudly hung a large banner on the front of the building for passing motorists to see. However, several big changes were lurking just ahead.
The first was caused by Covid. During the early days of the pandemic in April 2020, employees began making face masks in the Van Dyke plant’s ISO Class 8 clean room.
Ford’s global manufacturing and purchasing teams quickly sourced the necessary materials and equipment from its network of equipment manufacturers. A team of 30 UAW paid volunteers made masks in a clean room that normally housed delta robots that inserted retention pins in a valve body subassembly that controlled shifting. With extremely low levels of pollutants, the facility enabled the safe production of face masks for medical use.
One year later, Ford unveiled plans to rename and rebrand the 56-year-old facility the Van Dyke Electric Powertrain Center. “A longtime Michigan power train components plant now has a new name and an expanded production line that aligns with Ford’s commitment to an electric future,” proclaimed the announcement.
The facility was retooled to produce electric motors and electric transaxles for hybrid and fully electric vehicles such as the F-150 Lightning pickup truck.
“For more than 50 years, the Van Dyke Transmission Plant has produced suspension components and traditional transmissions for [our] internal combustion engine vehicles,” said John Savona, then-vice president of manufacturing and labor affairs at Ford Motor Co. “In the past 10 years, the plant added hybrid transmissions to its production mix. Now, the plant is transitioning once again to support Ford’s commitment to electrification.
“The advanced technology we are using at the Van Dyke Electric Powertrain Center is taking us to the next level for Ford’s electric future,” explained Savona. “The electric transformation we are making now is going to allow us to scale quickly as customer interest grows for our new electric vehicles.”“[Additive manufacturing] is used primarily to support spare parts in tooling,” says Mark Shkoukani, plant manager. “[For instance], if a spare ring or a gear on a machine is needed, it can be produced in-house instead of having to go to a vendor to buy.
“It also gives us flexibility to produce quick gauges or templates that can then go to vendors to produce the parts out of metal or other hard materials,” explains Shkoukani. “Plus, 3D printing gives us the added advantage of quickly testing and adjusting prototype parts. We also print kitting containers, kitting tool aids and templates for error proofing.”
Engineers at the Van Dyke Electric Powertrain Center are using AI technology to improve product quality.
“As a tool, AI can replicate, thus eliminating some destructive test sampling,” notes Shkoukani. “For example, reducing the frequency or eliminating a destructive test on an e-motor component varnish saves us both time and material. In 2022, [we] won a Ford Technical Excellence Award for [our] work in this area.”
Shkoukani and his colleagues use augmented reality technology for employee training applications. “We set up a virtual station so new operators can simulate the assembly process, learn what the job entails and get used to the environment before arriving at their future workstation,” he explains.
In addition, Ford Van Dyke engineers use data analytics every day to improve plant floor operations.
“We have a Global Data Insight & Analytics team establishing an automated dashboard to help analyze FTD and scrap data,” says Shkoukani. “Utilizing advanced control monitoring (ACM), which monitors all motions in CNC machines, enables us to improve throughput and volume by identifying wasted or redundant motions.”
Click here to learn more about the Assembly Plant of the Year award or to nominate a facility for 2024 (the deadline is May 1).