
With capacitive discharge welding, the heat-affected zone is localized to a small area around the weld.
Photo courtesy Heron Intelligent Equipment Co. Ltd.
Capacitive Discharge Welder Produces Quality Spot Welds
Capacitor discharge (CD) welding is a form of resistance welding that relies on energy stored in a large capacitor bank instead of drawing directly from a power distribution network. Because of this ability to rely on stored energy, CD welders have welding times that are short and concentrated, around 12 milliseconds, as opposed to about 100 milliseconds on a typical resistance welder. For mass production, such small time savings can really add up.
CD welders have many advantages. Weld nugget formation takes place during the first few milliseconds. CD welders release energy extremely fast, with large peak currents. More of the energy goes into weld formation and less into heating surrounding material. The heat-affected zone, where the properties of the metal have been changed from rapid heating and cooling, is localized to a small area around the weld.
The quick discharge rate of these welders also enables electrically and thermally conductive materials, such as copper or aluminum, to be welded. And, because energy is stored before release, CD welders deliver repeatable welds even when line voltage fluctuates.
Because the weld energy is concentrated for such a short time, there is less wear on the electrodes compared with conventional resistance welding. As a result, electrodes last four to 10 times as long, depending on the application.
Capacitive discharge power supplies are rated according to the amount of energy they store and the welding speed. The energy stored, expressed in watt-seconds, is the product of one-half the capacitance of the capacitor bank and the square of the applied voltage. However, the energy delivered to the electrodes will be less than this value because of losses in the primary and secondary circuits.
The length of the welding pulse depends on the materials to be joined. A short pulse is used to weld copper and brass, which require fast heating. A medium pulse is for welding nickel, steel and other resistive materials. A long pulse is used to weld resistive materials and to reduce sparking and electrode sticking.
The technology is widely used in the automotive, appliance and electrical equipment industries.
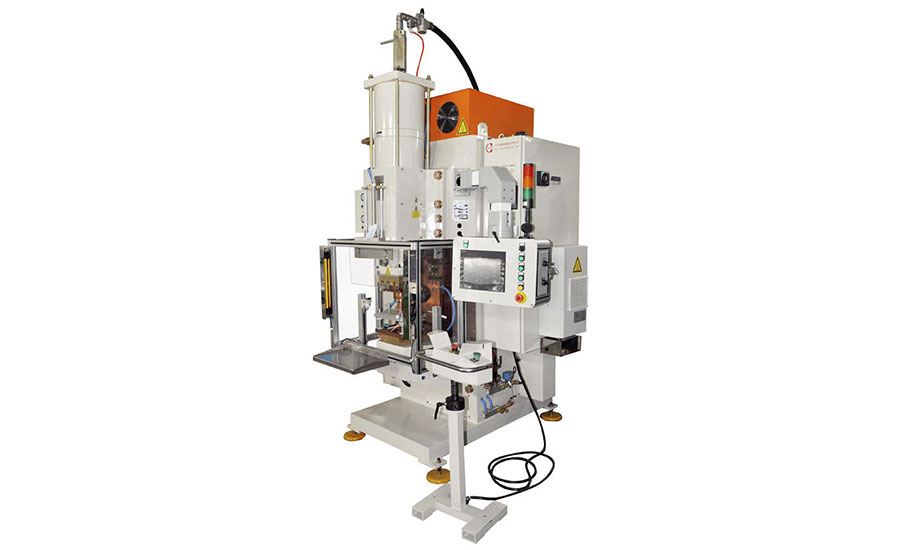
The DR-35000J medium-voltage CD welder is equipped with nonpolar metal film capacitors that resist decay. Photo courtesy Heron Intelligent Equipment Co. Ltd.
Heron Intelligent Equipment Co. Ltd. of Danville, IN, is a leading manufacturer of CD welding equipment. Among the company’s latest models is the DR-35000J. This medium-voltage welder is equipped with nonpolar metal film capacitors that resist decay. The volume of the capacitor is 70,000 microfarads, and the rated capacity is 100 kilovolt-amps. The weld pulse can be set from 5 to 30 milliseconds, and the capacitor bank takes only 1 second to charge. The transformer does not require water cooling.
The welder can apply a maximum force of 34,000 newtons. It has a throat depth of 400 millimeters and an arm gap of 400 millimeters.
Heron also manufactures resistance welding equipment, the BTM Tog-L-Loc system for sheet metal clinching and the AKH Fas-ner self-pierce riveting system, a mechanical fastening process for joining two or more metal sheets that are difficult to weld, such as aluminum and steel.
For more information on welding, clinching and riveting equipment, click www.heron-welder.com or visit the company’s booth at The ASSEMBLY Show South, which will be held April 30-May 2, 2024, at the Music City Center in Nashville, TN.
Besides test systems, you’ll find some 150 suppliers of automation, fastening tools, robotics, parts feeders, presses and other assembly technologies. For more information, visit www.assemblyshowsouth.com.