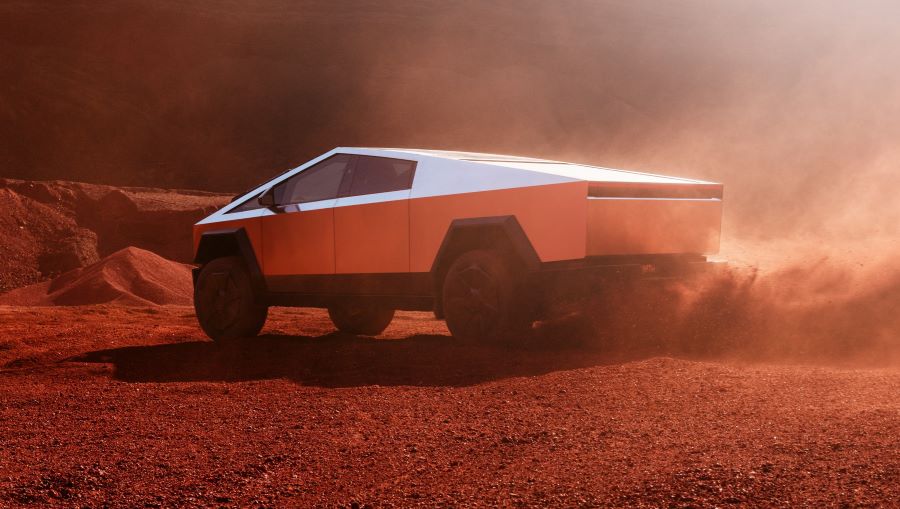
Tesla’s New Cybertruck Features Modular Wiring
Tesla Inc.’s highly anticipated Cybertruck features a radical shape that’s unlike other pickup trucks on the market. But, there’s more to it than meets the eye
Inside, the stainless steel-bodied vehicle contains a state-of-the-art steer-by-wire system. Out-of-the-box thinking is also behind a 48-volt electrical system and a modular wiring system.
Instead of a central controller, the Cybertruck is equipped with local controllers. In adition to reducing complexity, cost and weight, the distributed system enables Tesla to bypass the expensive and time-consuming process of assembling and installing traditional wiring harnesses. The flat, modular wiring harnesses are also designed for automated assembly.
According to the automaker’s U.S. patent application for a “wiring system architecture,” the new system “includes a plurality of devices, wherein the devices are connected to a backbone section that has an outer sheathing, a first conductor disposed within the outer sheathing, a second conductor disposed within the outer sheathing, a pair of inner sheathing members disposed within the outer sheathing and located on opposing sides of the at least one conductor, the inner sheathing members configured to electrically insulate the first conductor from the second conductor, and a shield member disposed within the outer sheathing.
“Traditional car wiring for vehicles are piecemeal solutions. Typically, there are different wiring harnesses that connect each different electrical component to a central battery or power source. Each component receives power, but requires multiple wiring harnesses for communication and signals. The total length of the wire may be many miles within a single vehicle.
“These wiring harnesses typically consist of multiple round conductors that are not rigid. Round conductors are not optimal for transmitting current and the lack of rigidity of traditional wiring harnesses requires assembly into the vehicle using human hands, which can be a slow process. Further, connecting each component to the central battery is not optimized on an automobile level.
“Hence, there is a need for wires and a wiring-system architecture that overcomes the aforementioned drawbacks….”
The patent filing relates to “a wiring system architecture and the cables and connectors necessary to implement the architecture. The overall wiring system disclosed herein approaches wiring in a different manner than traditional automotive wiring architectures.
“Traditional automotive wiring architectures often have many miles of cables snaking from centralized controllers and power sources to devices through the vehicle. This new architecture reduces the number and length of cables, and moves certain controllers into subassemblies which then control one or multiple devices present in the vehicle. To achieve power and signal transmission, new cables and connectors have been created….
“In this new wiring architecture, subsystems are packaged and defined in one or multiple assemblies in certain embodiments. For example, a door assembly might contain one controller (or hub) that controls multiple devices, such as locking components, lighting components, audio components, etc.
“In addition to decreasing the number and length of wiring needed, the ability to create these subassemblies and then connect them to the wiring architecture backbone will decrease assembly time during general assembly, which is very desirable to increase productivity in a vehicle manufacturing process. The subassembly may be created ahead of general assembly with only the connection between the door subassembly and subsystem made and verified during general assembly.”
Tear-down specialist and lean manufacturing guru Sandy Munro recently moderated a candid discussion about the Cybertruck with several Tesla engineers, including Lars Moravy, vice president of vehicle engineering, and Pete Bannon, director of low-voltage electronics and hardware engineering.
They explained how the Cybertruck uses an ethernet loop, dubbed an “etherloop,” that connects multiple high-speed controllers together, while reducing the weight and complexity of wiring.
“Between the etherloop and 48 volts, wiring mass is down significantly,” Bannon points out. “The etherloop connects all of the high-speed controllers together...The number of wires that go across the car has been reduced dramatically, even though the number of end points went up. The total mass of wires is way down and the average length of wires is significantly shorter.”
In fact, Bannon claims that “high-powered harness mass went down by 84 percent.” That’s despite that fact that there are 50 percent more end points in the Cybertruck vs. the Model 3.
According to Bannon, the etherloop system enables Tesla to reduce the amount of wiring needed by 68 percent. By comparison, he says the Cybertruck only has 155 wires vs. 490 wires in the Model 3. However, there are 368 end points in the Cybertruck vs. only 273 in the Model 3.