In 1969, Canadian Walter Sellick and his sons Howard and David converted a Ford 4500 industrial tractor into a forklift for outdoor use. Their reconfigured machine could lift 6,000 pounds.
That simple idea turned into a family business, Sellick Equipment Ltd., in Harrow, ON, that manufactures rough-terrain forklifts and truck-mounted forklifts. Today, more than 11,000 Sellick-built machines are in use worldwide, and the company has more than 200 dealers throughout North America. And, the company is still being run by a Sellick, Walter’s grandson, Colin.
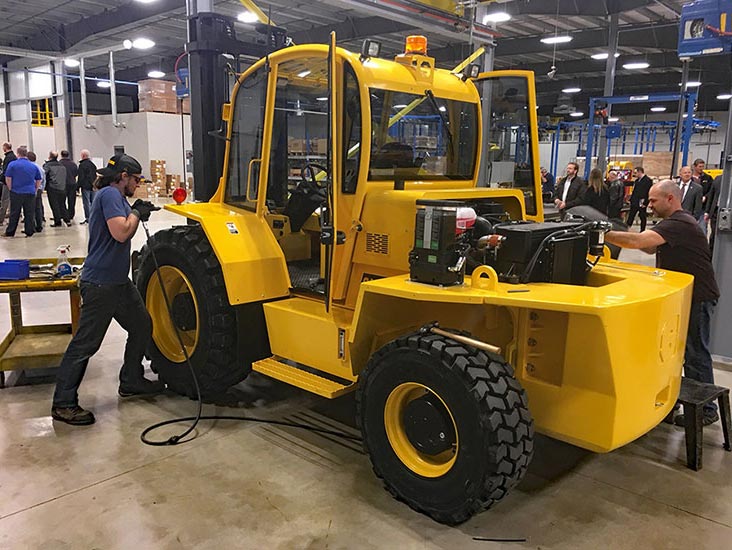
Sellick Equipment manufactures rough-terrain forklifts and truck-mounted forklifts. Photo courtesy Sellick Equipment Ltd.
The company’s forklifts range in capacity from 5,000 to 16,000 pounds and feature the Sellick See-Thru mast with lift heights of up to 30 feet. All models are available with four-wheel drive. Standard features include operator guarding, full instrumentation and lighting. Options include full cabs with heat and AC, hydraulic fork movement, and a variety of fork lengths and carriage widths.
In 2018, the company built a new $21 million assembly plant in Harrow. Among other things, the 126,000-square-foot factory was equipped with a new machining center comprising CNC laser cutting, milling, and turning machines; automated storage and retrieval systems for raw materials and aftermarket parts; metal preparation equipment; and a paint line.
Another priority for the new factory was to find better ways to move and position heavy, welded subassemblies around the shop floor. To find the best technology, Sellick engineers visited several tradeshows, including the Fabtech show in the United States, where they tested systems from multiple companies. In the end, equipment from one company stood out: Gorbel Inc. in Fishers, NY.
“When it came down to ease of use, it was Gorbel by far,” says Sellick. “There was no one that was even close to having a system that worked as well or easy as the Gorbel system.”
At Sellick’s old facility, engineers had to deal with multiple obstacles to movement, including height limitations and ceiling restrictions. Columns populated the shop floor every 15 feet. Very little movement was possible while assembling the company’s products, and a forklift was needed for some processes.
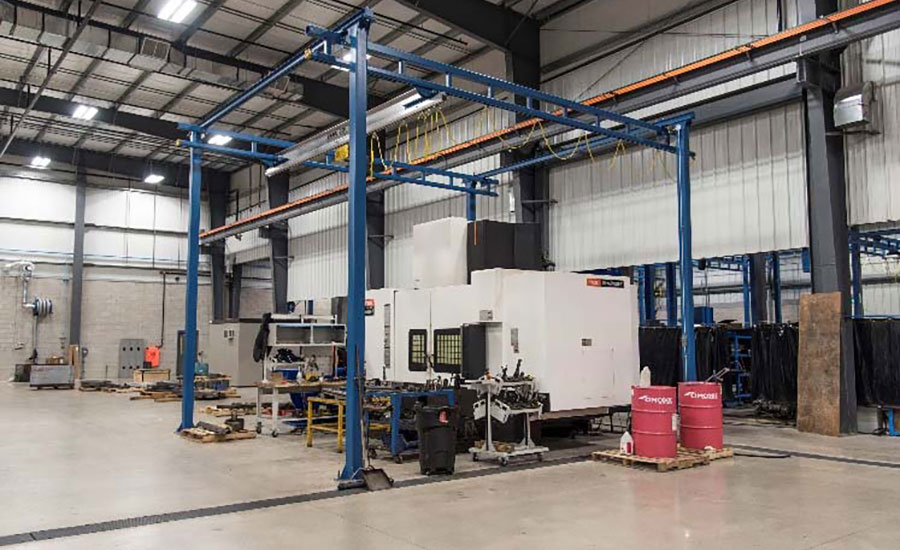
Two Gorbel free-standing workstation cranes service milling machines. Photo courtesy Sellick Equipment Ltd.
The new factory opened up opportunities to better the assembly processes. Two Gorbel free-standing workstation cranes were installed in the fabrication area to service the milling machines.
Workstation cranes are a type of industrial crane that consist of a moving bridge that runs across parallel runways. On the bridge, there is commonly attached a hoist or other lifting devices such as a manipulator or intelligent lifting device that travels across the bridge. Bridge cranes cover rectangular work areas.
A free standing bridge crane is intended to be bolted to the floor and to support loads that will be moved vertically and horizontally. One worker can manipulate the load along a series of tracks, including curves and monorails, inside a closed system. This design works well in an area with limited headroom or a ceiling that is not strong enough to support a mounted bridge crane.On the assembly line, an eight-bay Gorbel free-standing workstation crane services 16 welding cells. In addition, the assembly line was also equipped with a 140-foot free-standing workstation crane with four aluminum bridges; two 2-ton cranes; and two 1-ton cranes.
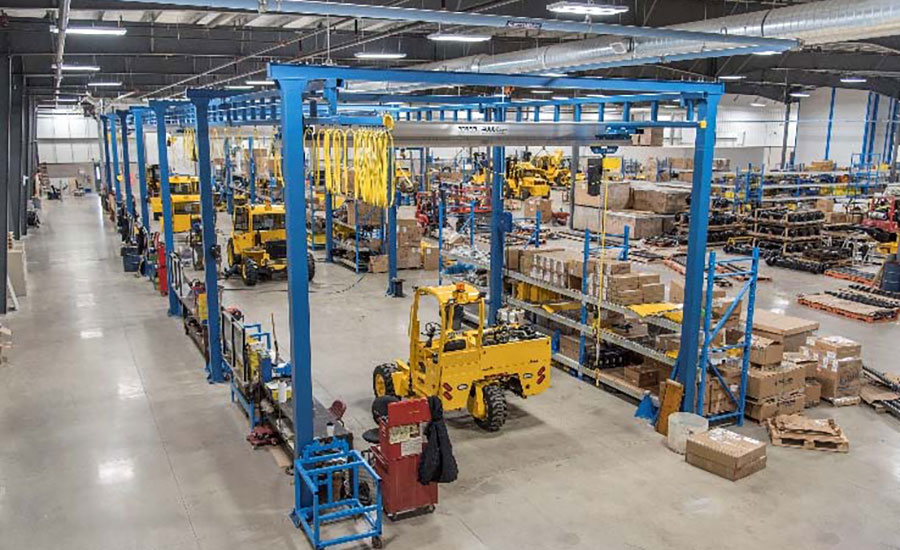
The assembly line is equipped with a 140-foot free-standing workstation crane with four aluminum bridges; two 2-ton cranes; and two 1-ton cranes. Photo courtesy Sellick Equipment Ltd.
Productivity has increased because workers are able to freely move the product down the 140-foot long, 20-foot wide assembly line without restrictions. This has opened up areas for part storage and has helped to smooth out the workflow processes for the assembly operators. During assembly, two speed hoists are used to position parts.
Assemblers at Sellick Equipment are pleased with the Gorbel systems’ ease of use under load. They are especially pleased that the load stays where it should with no drift or slide in the aluminum bridge to make precision part placement easier.
For more information on cranes and other ergonomic positioning equipment, visit www.gorbel.com.
ASSEMBLY ONLINE
For more information on ergonomic handling equipment, read these articles:
Lifts Speed Up Engine Assembly
Intelligent Assist Devices
Stronger, Safer, Faster, Smarter