Bizerba SE & Co. makes slicing, weighing, packaging and labeling equipment for commercial kitchens and food manufacturers. Based in Balingen, Germany, some 46 miles southwest of Stuttgart, Bizerba is a family-run business with 158 years of history and high quality standards. At the same time, however, the company continues to innovate and expand internationally.
Today, Bizerba has approximately 4,100 employees worldwide, including three production facilities in Germany. A vertically integrated manufacturer, Bizerba handles the entire process of making its products, from machining aluminum blanks through to final assembly.
Bizerba’s factory in Messkirch, Germany, makes slicing machines for bistros, delis, groceries and other users. The company has designed machines to cut bread, vegetables and meat. Some slicers are quite sophisticated, with electronics for networking and operator support.
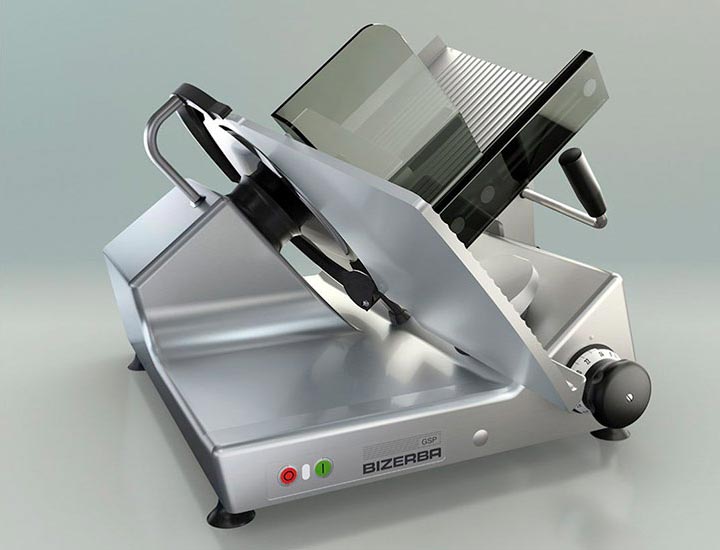
Bizerba’s inclined slicing machines are particularly popular in the U.S. Photo courtesy Bizerba SE & Co.
In the summer of 2021, Bizerba received an order from an American company for a five-digit quantity of slicers to be delivered by the summer of 2023. Specifically, the customer wanted inclined slicing machines, which are particularly popular in the U.S. Because of the inclined arrangement of the carriage, the material to be sliced does not have to be pressed by hand, but is held firmly in place by gravity. This makes work easier for the operator, especially with heavy material. It also ensures that slices are always of the same thickness.
The order was, of course, an organizational challenge. It represented a six-fold increase in production volume for that particular model and a doubling of the total turnover at the Messkirch assembly plant.
“We had to increase production capacity drastically and as quickly as possible,” explains Jochen Lude, production planner at the factory. “That meant hiring new employees, but also expanding the assembly stations. Although we had our own production equipment, it was already being used elsewhere.”
Bizerba needed to increase capacity—and do so rapidly. Ultimately, the company opted to purchase finished assembly workstations from MiniTec GmbH & Co.
Since it was founded in 1986, MiniTec has grown from a specialist for miniature guides into a leading technology company. Based in Schönenberg-Kübelberg, Germany, MiniTec offers an array of products, including structural aluminum profiles, linear motion systems, workstations, conveyors and machine guarding products. The company also designs and builds automated systems, assembly stations and even entire lines. It has 11 locations in Germany, France, Great Britain, Spain, Slovenia, China and the United States.
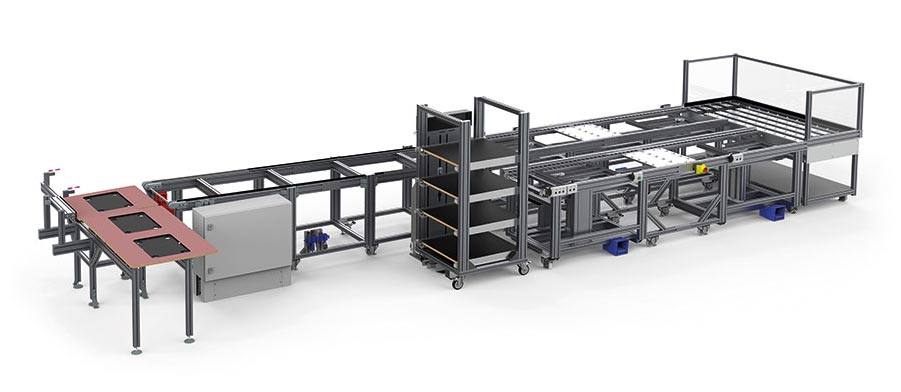
Due to the limited space available, assembly stations were arranged in a U-shaped line. Photo courtesy MiniTec GmbH & Co.
Division of Labor
Bizerba had already been working successfully with MiniTec for many years. A key factor in the decision was MinTec’s modular aluminum profile system, which would enable Bizerba to reconfigure and redeploy the new equipment once the order was completed.
Bizerba wanted to more than just add capacity; it also wanted to speed up the process of assembling the slicers. Previously, one employee completely assembled a slicer. Aside from enormous space requirements, this strategy had other disadvantages. For example, collisions often occurred because each employee worked at a different pace, and a common tool needed to assemble the slicers was never ideally positioned.
In the new line, assembly would be carried out by four employees, in four cycles, at assembly islands. The walking and gripping paths for each employee would also be optimized.
The project started in October 2021, and it quickly became clear that the new assembly islands would initially have to be implemented without automation to stay reasonably on schedule. With that decision made, implementation went quickly.
“We ordered in December and were already able to set up the first two lines at the end of February, albeit still without automation—that was immense!” says Lude. “Together with MiniTec, we then successively set up further lines in a six-week rhythm and added automation to the existing assembly islands. By July, we already had the complete assembly line running, including automation.”
This approach enabled Bizerba to ramp up assembly capacity with new manpower at an early stage.
Lude praises MiniTec’s flexibility and willingness to cooperate. “Of course, it was rather untypical that we first purchased partially completed assembly systems, and we were glad that MiniTec went along with us,” explains Lude. “At the same time, a floor renovation took place during the course of the project, and we continued to produce completely. This meant that MiniTec’s assemblers had to set up the new line within this area during normal production. These were difficult conditions, and I would like to commend the MiniTec installation team on this.”
To make the rapid schedule possible, the project team from Bizerba was able to exchange information directly with the MiniTec design engineers at any time. “The response times were always very short,” says Lude. “If we had a question in the morning, there was usually an answer and a proposed solution by lunchtime, at most the next morning.”
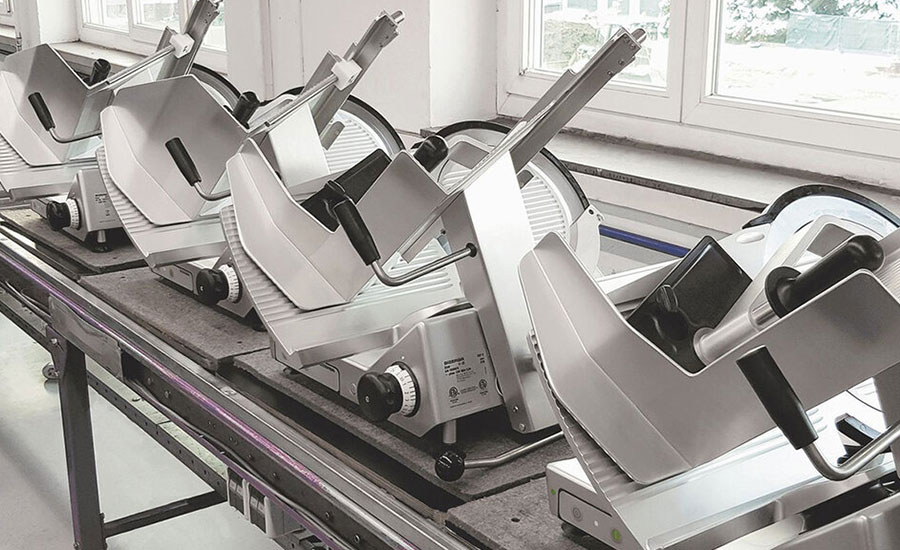
Fully assembled slicers queue up for final inspection and then shipping. Photo courtesy MiniTec GmbH & Co.
Everything in Flow
In the slicer assembly line, 350 components are assembled in four steps. Due to the limited space available, assembly stations were arranged in a U-shaped line instead of straight line. The U-shaped arrangement gives assemblers a little more space, and they can also exchange ideas while working because they are facing each other.
At the start of the line, preassembled aluminum housings are brought to the first workstation by transport trolley. The trolley is pushed onto a fork and lifted to the desired removal height by means of a lift. From here, the employee pushes the housing via a roller bar onto his station and pneumatically lifts it, including the workpiece carrier, to his desired working height.
After he has completed his work, he lowers the housing and pushes it over to the next assembly station. To move the assembly to the third workstation, MiniTec implemented an automatic transfer unit. The employee at the second workstation pushes the device to the right. In doing so, he triggers a sensor, which places the device on a conveyor. The employee at the third workstation can then request it by pressing a button.
Once assembly has been completed at the third workstation, the worker lowers it again and transfers it to the last workstation. Once assembly has been completed there, the fully assembled slicer is transferred to an existing roller conveyor, which travels along a wall to a central elevator.
Here, MiniTec had a problem to solve, because the control system of the roller conveyor was not to be interfered with. Therefore, MiniTec developed an automated outfeed conveyor. When work is completed at the final workstation, the assembler pushes the unit to the right. A sensor responds, and a toothed belt conveyor starts to run. At the same time, the roller conveyor is blocked by stoppers, so the slicer can be discharged onto it. On the roller conveyor, the slicer is fed to an inspector and then to a laser marking station, which creates a rating plate. The slicer then goes down one floor to shipping via the elevator.
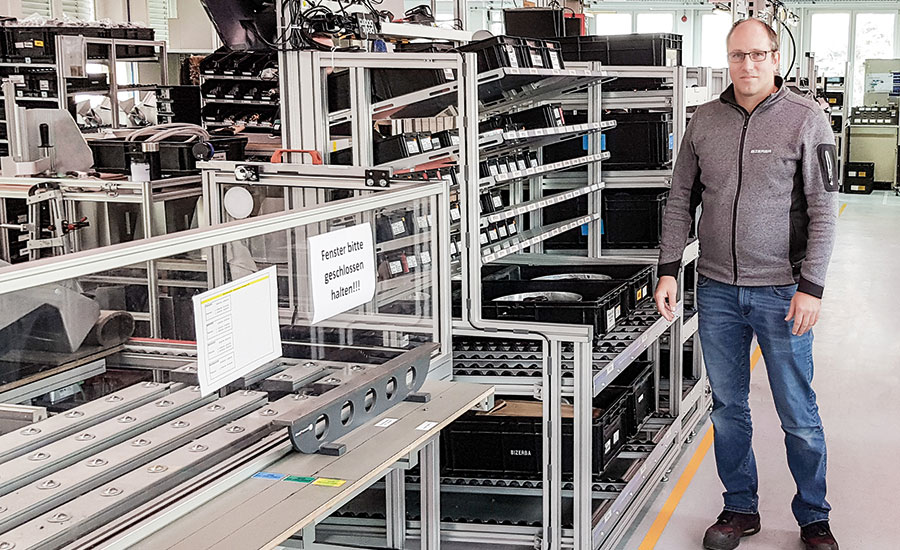
Parts replenishment is handled by flow racks and a kanban system. Photo courtesy MiniTec GmbH & Co.
Kanban for Material Supply
A micrologistics specialist ensures that the required parts and materials are always available at the assembly stations. Small parts, such as threaded fasteners, are brought in by employees from a central warehouse to an intermediate area, from where micrologistics specialist collects and distributes them using carts. Bizerba relies on kanban control for material supply. In the case of the preassembled housings, this is done on sight. As soon as the micrologistics specialist notices that the cart at the first workstation is becoming empty, he replaces it with a full one.
All other components resupplied via kanban cards on each container. The material number is married to the bin, a bar code and a storage location. When the first box becomes empty, the worker places it onto a return rack, and a second box slides in. The micrologistics specialist takes the first box and brings it to the central transfer station. The empty crate then goes from there to the main warehouse, where it is refilled and sent back to the transfer station. MiniTec designed and built all the transport carts for the process.
The expansion of production and the redesign of the assembly process was a complete success. “Thanks to the rapid and flexible implementation of the assembly islands with MiniTec, we were able to produce the order from the U.S.,” says Lude. “In addition, we were able to significantly accelerate the output of devices per shift by switching to work-sharing assembly.
“There are hardly any downtimes or congestion phases,” he continues. “Of course, this is also due to the improved ergonomics. The tool is now always in the same position. The employee gets a certain routine. By dividing up the overall work content, it is also easier to train new personnel because the scope of work for the individual is no longer so large. He only has to know a section of the cutting machine. This is a big advantage for us in the current situation, where we need 25 percent more personnel.”
Based on the positive experience with MiniTec, Lude is already thinking about additional projects. These will primarily involve digitalization in assembly, with technology such as the MiniTec SmartAssist worker assistance system and the integration of RFID tags.
ASSEMBLY ONLINE
For more information on workstations, read these articles:
Electrical Equipment Manufacturer Benefits From ESD-Safe Work Benches
Comparing Structural-Component Systems
Automotive Supplier Creates Carousel Assembly Line From Modular Components