The Industrial Internet of Things (IIoT) promises to provide real-time data, intelligent interconnectivity and flexible automation. For many organizations, the opportunity to realize the value of Industry 4.0 is still on the horizon. At Salvagnini, however, an overarching commitment to process optimization and efficiency is yielding tangible benefits today.
Based in Sarego, Italy, Salvagnini manufactures equipment for processing sheet metal, including punching machines, panel benders, press brakes and laser cutting machines. The company has installed more than 7,000 systems in 75 countries. Salvagnini employs some 2,000 people across five manufacturing plants, 35 service centers and 23 operational sites around the world.
“Salvagnini has been designing, manufacturing and selling flexible machinery and systems for sheet metal manufacturing since 1963,” boasts Tommaso Bonuzzi, sales director at Salvagnini. “Our R&D team is constantly working to implement the most advanced, pioneering technology to increase the potential of our systems.”
“Salvagnini systems are complex,” adds Alessandro Bano, commodity manager at Salvagnini. “They demand high-quality standards and conformity with the certifications and regulations established in all of the markets we serve.”
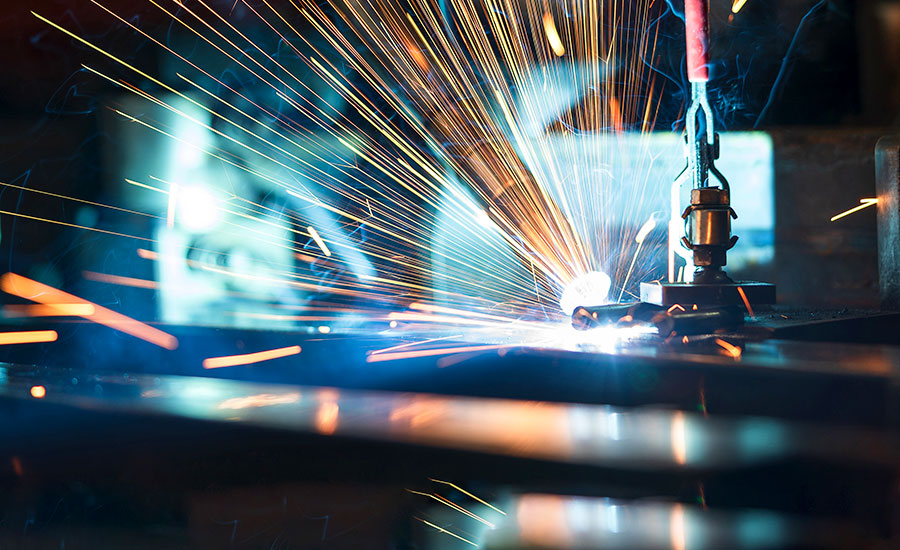
Salvagnini manufactures laser cutting machines and other equipment for processing sheet metal. Photo courtesy Salvagnini
An IIOT Imperative
The idea of a connected, integrated factory is a pillar of Salvagnini’s approach to processing sheet metal. As early as the 1980s, Salvagnini began developing the concept of the Automatic Job Shop: a lights-out factory with interconnected, automatic machines that communicate directly with a customer’s enterprise resource planning system.
“Our aim is to create a cooperative, integrated ecosystem where machines work in synergy,” Bonuzzi says. “This reduces the occurrence of errors while optimizing the performance of the entire plant.”
To ensure seamless collaboration among operators, machines and instruments, Salvagnini prioritizes the use of IIoT, cloud software, big data and interconnectivity.
“We must guarantee high connectivity standards and secure communications between on-site sheet metal machining systems and servers in the cloud,” says Bano.
High-speed connectivity is essential for exchanging data with factory-floor systems and smart sensors. It also enables a wealth of information sharing. “Today, our machines [send production data] to the cloud, and they also transfer real-time information to each other and with ERP systems,” explains Bonuzzi. “The feedback from our customers on these initiatives has been very positive, both in terms of greater possibilities for services and the opportunity to boost productivity of the whole process.”
For that reason, Salvagnini cannot compromise on connectivity, which is why the company reached out to Molex after encountering stability issues with a legacy connectivity technology provider.
“We turned to Molex after dealing with communication loss issues on an EtherCAT line, which is the backbone of our machines,” says Bruno Sambi, head of the technical department at Salvagnini. “Together, we tackled the wiring issue and investigated different connector types to determine how best to achieve higher stability and connection quality.”
Based on their experience with Industrial Ethernet architecture and devices, Molex engineers found and fixed the problem. “Trying to determine the root of our issue was complicated,” remembers Bano. “Molex engineers quickly analyzed and solved the problem. They also offered a unique solution for Ethernet, EtherCAT and Canbus cables, which we later adopted at all of our production sites in Italy.”
Flexibility was a major consideration, since the various components of Salvagnini’s systems often are adapted to different production configurations. At the same time, Salvagnini engineers wanted standardized parts for its equipment to simplify sourcing and parts replacement.
“The initial catalyst for working together was Molex’s suite of existing connectors, cables and cord sets,” says John Newkirk, vice president and general manager for industrial solutions at Molex. “We were an attractive partner from an electromechanical and connector standpoint, which gave Molex a window into Salvagnini’s longer-term needs and requirements.”

Salvagnini is developing the concept of an Automatic Job Shop: a lights-out factory with interconnected, automatic machines that communicate directly with a customer’s ERP system. Photo courtesy Salvagnini
According to Luciano Rosa Marin, senior business development manager at Molex, the company’s knowledge of Industrial Ethernet architecture and devices played a pivotal role in working with Salvagnini.
“There are three main reasons for our competitive advantage, starting with our wide portfolio of products and local technical support, which quickly identifies critical issues on Industrial Ethernet connections,” he says. “Moreover, our ability to find new solutions and implement them in a short time has led to an open and fruitful relationship that extends to the collaborative design of Salvagnini’s next-gen machine design architectures.”
Another factor was Molex’s customer service network. “Molex impressed us with the quality of its products and its ability to conform to our standards,” adds Bano. “The responsiveness of their staff in providing technical engineering explanations also helped guide our own operational model and customer approach.”
Both companies worked together to reduce the size of connectors without compromising the reliability or quality of communications. “We are constantly improving the quality of Molex’s Ethernet connecting cables,” Rosa Marin notes. “Another major area for us is customized solutions that require a high mix of connecting cables with a variety of lengths and connector combinations.”
In one case, Molex devised an overmolded connector, which is different than conventional bayonet systems, to ensure high-speed communications stability in compact environments.
“The collective engineering teams designed a compact, overmolded connector for Ethernet patches with an IP67 rating for reliable performance in highly rigorous, wet environments,” says Rosa Marin.
Another example of teamwork is a system for the cameras on Salvagnini’s L3 and L5 laser cutting machines. These cameras acquire the image of a piece of sheet metal on the worktable and transmit it via software as a drawing exchange format (DXF) vector file to display the starting format for a new cut.
“These cameras have to be powered continuously,” adds Bano. “You also need real-time communications to send video data to the system for rapid processing.”
Molex designed a new system, consisting of a single cable that connects the cameras to an electrical power supply via a switch and an RJ45 connector.
“Delivery times for this new product were very fast,” notes Bano. “In addition to reducing the size and number of cables, we also improved the speed of communications between the camera and our system.”
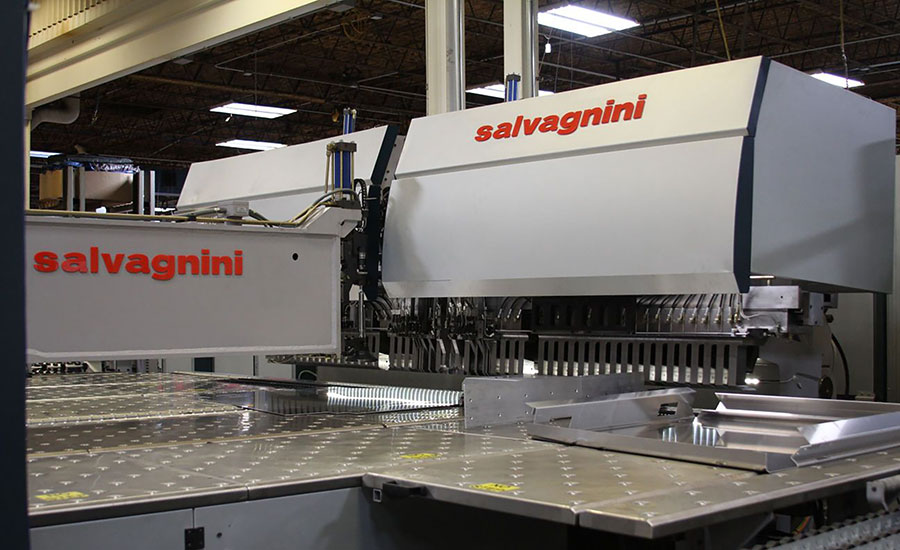
To ensure collaboration among operators, machines and instruments, Salvagnini prioritizes the use of IIoT, cloud software, big data and interconnectivity. Photo courtesy Salvagnini
Global Reach
Molex’s ability to reach across the globe for answers while leveraging a local support team keeps Salvagnini on the cutting-edge of IIoT advancements.
“Having a strong local sales engineering presence, augmented by technical business development, is key,” Newkirk says. “Molex applies a lot of technical expertise to address customer requirements, resulting in the development of products that are relevant to what they need most.”
For Salvagnini, this long-term relationship has translated into benefits for both organizations. “Together, we solve any issue that may come up, while developing new solutions to promote and create mutual value,” adds Sambi. “We hope that our work with Molex evolves into an even deeper collaboration to create increasingly innovative and well-performing solutions.”
During the COVID-19 pandemic, Salvagnini encountered delays in coding new products, which entailed months-long wait times in some cases. To alleviate this burden, Molex ramped production of standard parts in different sizes, so they could be adapted quickly to address specific customer needs. Thanks to the presence of a Molex distributor in Italy, these parts are stored locally to ensure an ample supply for both in-house production and spare parts. Additionally, the design of a standard wiring system gave Salvagnini a one-year overview of supply to support strategic order planning.
Accelerating Industry 4.0
Molex and Salvagnini remain steadfast in the pursuit of technology and service excellence. “Molex brings strong capabilities in industrial communications as well as a global point of view,” says Rosa Marin. “Salvagnini has deep knowledge of the applications related to these technologies, as well as what is needed to develop a new industrial Ethernet network architecture.”
The companies’ combined Industry 4.0 focus guides the design, development and delivery of more compact, IP67-rated products to support smaller and more powerful machines that must perform reliably in the most rigorous environments. Opportunities to improve machine diagnostics and expedite repair also are being explored.
“We have a suite of hardware and software products that are very relevant to the IIoT space,” Newkirk adds. “Molex will continue to apply a deep knowledge of solderless terminals, circular cables and industrial electronics that enable new levels of flexible automation.”
As a result, Molex is becoming Salvagnini’s preferred provider for next-generation automation communications, including single pair Ethernet, time-sensitive networking, and fail safe over EtherCAT.
“Our ultimate goal is to go beyond manufacturing and offer customized solutions to support our partners in their own evolution,” concludes Bonuzzi. “Having interconnected machines and available data to analyze and use for future choices is essential. We see huge potential for growth across the vast IIoT ecosystem, both in terms of the technical side of our systems and the business applications of our consulting services.”
ASSEMBLY ONLINE
For more information on industrial networking, read these articles:
BMW to Use Molex Electrical Interface on Next-Generation EVs
Connectivity for the Factory of the Future
New Hardware for Industry 4.0