In the late 19th and early 20th centuries, convicts in the U.S. and the U.K. were often forced to crush rocks with picks and sledge hammers. The task was more than punishment or “rehabilitation.” Prisons sold the quarried stone and crushed gravel as profitable commodities.
These days, the job of crushing rocks is done by big, heavy machines. One of the world’s leading manufacturers of such equipment is the Minerals Processing Systems (MPS) division of Terex Corp. Terex MPS manufactures crushers, washing systems, trommels, conveyors, cranes, concrete mixers, and machinery for processing wood and biomass. The company’s machines are used in construction projects, quarrying and mining applications, demolition and recycling operations, and the landscaping and biomass production industries. Terex MPS machines can process hard and soft rock, sand and gravel, ore and industrial minerals.
The company’s brands include Canica, Cedarapids and Simplicity. Two of those brands—Canica and Simplicity—are more than 100 years old.
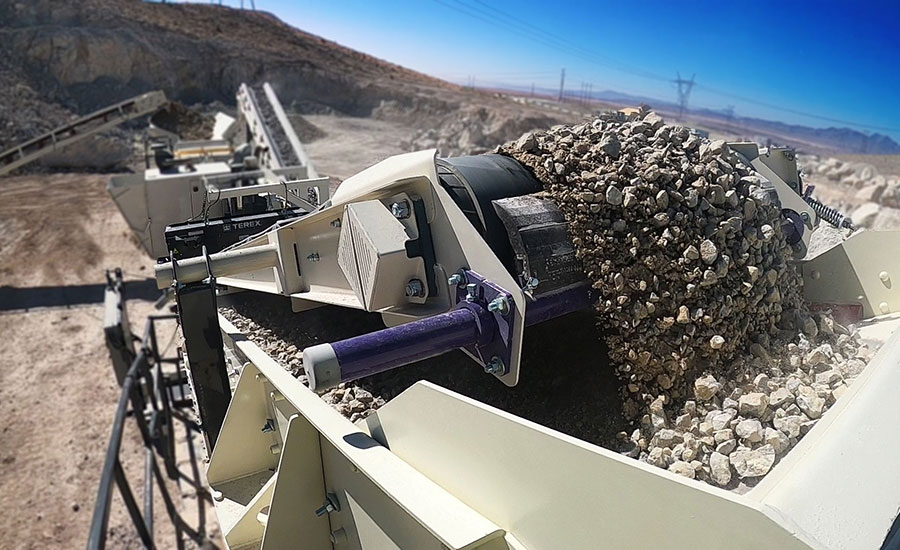
Rock crushing equipment must be designed to withstand the harshest conditions: heavy loads, high forces, and tremendous shock and vibration. Photo courtesy Terex MPS
Needless to say, such equipment must be designed to withstand the harshest conditions: heavy loads, high forces, and tremendous shock and vibration.
When Terex MPS needed a reliable and flexible system to measure stress on its stone crushing machines, it turned to Hottinger Brüel & Kjær (HBK) for help. Based in London, HBK was founded in 2019, with the merger of German company HBM and Danish company Brüel & Kjær. Brüel & Kjær specializes in technology for measuring sound and vibration. HBM develops instruments for measuring reliability, durability, propulsion efficiency and weighing.
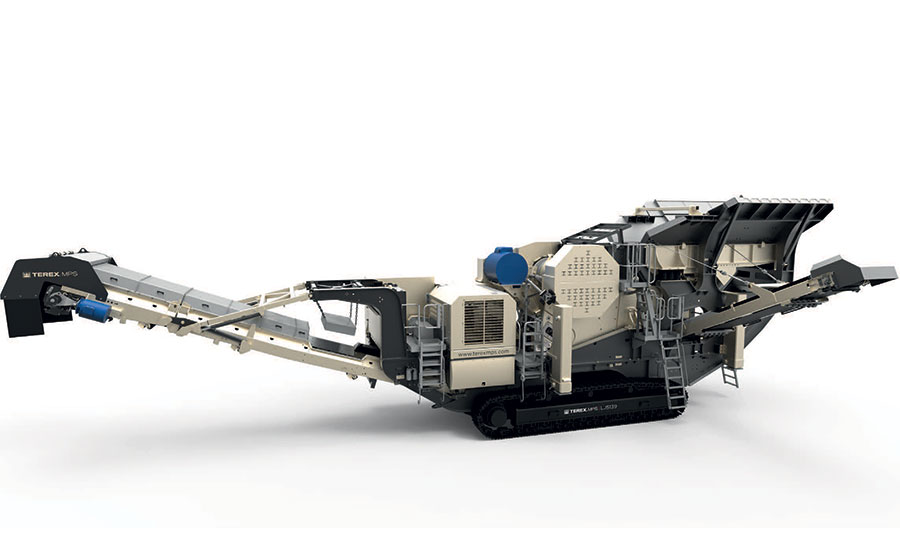
Designed for use in quarries, the LJ5139 mobile jaw crusher weighs more than 115 tons. Photo courtesy Terex MPS
Terex asked HBK to consult on the company’s new LJ5139 mobile jaw crusher. Designed for use in quarries, the tracked machine weighs more than 115 tons. The chassis is subject to high loads when moving on uneven surfaces. In addition, the hopper and feeder receive high impact forces when large stones, with a volume of up to 1 cubic meters, are dropped into it by an excavator. The machine itself is subject to forces of up to 8,000 kilonewtons during the crushing process.
“To deal with these issues, we initially used finite element analysis during the design process and verified the results in the field using strain gauges,” says Ian Boast, chief engineer at Terex. “Previously, we relied on rented [test and measurement] equipment, but we were keen to invest in our own equipment for increased flexibility.”
The rented equipment had another problem. It was susceptible to noise interference from surrounding equipment. This was particularly problematic, since the loadings in the crusher are often random and transient in nature, which could potentially cause confusion and false results. In addition, the quarry environment was quite dusty. This limited test options on site, and it also meant that engineers had to take special care of the instruments.
A Rugged Instrument
After studying the issues, HBK specified its SomatXR series of data acquisition devices, which are particularly suitable for use in harsh environments. Specifically, HBK suggested the SomatXR MX1615B-R module and related accessories, which included RF-9 strain gauge rosettes.
The SomatXR is protected from humidity, dust, shock and vibration. It can withstand temperatures of -40 to 80 C. It carries an IP67 protection rating against dust and water. And, it is vibration- and shockproof in compliance with MIL-STD202G (10 g and 75 g respectively). Because the amplifier is located close to the measuring points, signal interference is reduced.
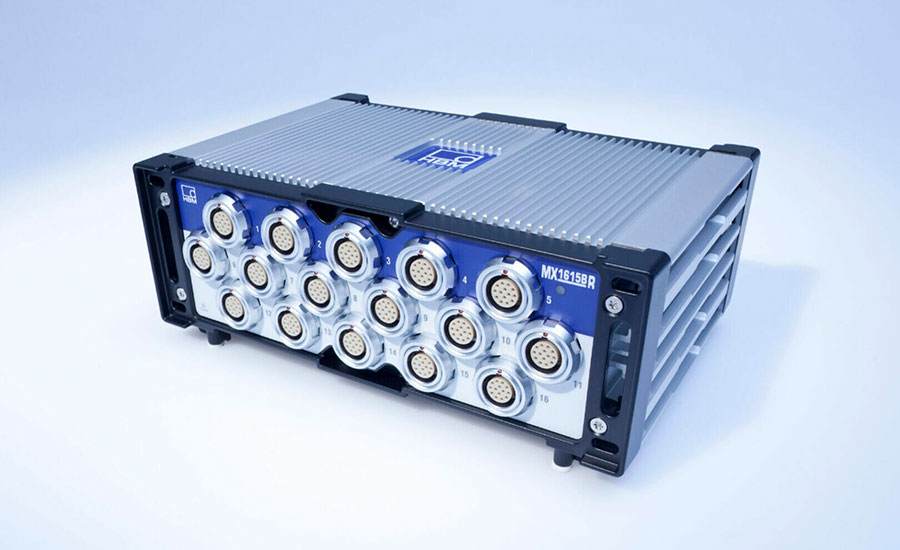
The SomatXR data acquisition system is protected from humidity, dust, shock and vibration. Photo courtesy Hottinger Brüel & Kjær
The modular system can be used in various applications, such as mobile vehicle testing, stationary measurements, and structural health monitoring. The modules can be easily combined in centralized or distributed configurations. The system lets engineers interactively perform testing and measuring tasks, and always have complete control. However, it’s also possible to select an autonomous “black box” recording mode for long-term testing.
The system can be integrated with other software programs, such as LabVIEW, Visual Studio.NET or CANape. The modular architecture lets engineers implement their own measurement system with a data recorder or with a PC. In addition, SomatXR modules can be integrated into test bench applications or ECU optimization software in various ways and flexibly combined with other testing modules.
For Terex engineers, a major advantage of the system is its ability to perform long-term testing under extreme conditions. The device will not lose measurement data due to unforeseen events, such as power failure. The SomatXR system continuously records data. This means that should a failure interrupt a test, recorded data up until that point will be saved. The system continues to log data automatically, after a power interruption, without any need for user interaction.
“The analysis software that HBK supplied is intuitive and easy to understand. The user friendly visualization module allows us to view live data as it is being recorded on site,” says Boast. “Also, we are now able to create custom indicators based on live calculations, since we receive live figures of the toggle plate load while the crusher is running.
“Another helpful feature is that we can continually change the display on the screen while we are logging data, which allows us to monitor each gauge in turn as a full-screen graph. As a result, we can instantly identify high loads. The post-processing capabilities of the software are also very impressive; there are a variety of ways to filter and trim data before exporting in various formats.”
For more information on test and measurement equipment, visit www.hbkworld.com.
ASSEMBLY ONLINE
For more information on data acquisition technology, read these articles:
Four Sources of Inaccuracy in Sensor Measurements
Device Monitors Metal Stamping Press
Data Logger Plays Key Role in Design of Solar-Powered Race Car