In machining, a tipped tool is any cutting tool in which the cutting edge consists of a separate piece of material that is brazed, welded or fastened onto a body made of another material. In the latter case, the cutters are called inserts, because they are inserted into the tool body. Tipped tools allow each part of the tool, the shank and the cutter, to be made of the material with the best properties for its job. Common materials for cutters include cemented carbide, polycrystalline diamond, and cubic boron nitride. Tools that are commonly tipped include router bits, end mills and face mills.
The advantage of tipped tools is that only a small amount of material is needed to make the cutter. As a result, manufacturing the insert is easier than making the entire tool out of the cutting material. This also reduces cost, because the tool holder can be made of a less-expensive and tougher material. In fact, a tipped tool is often better than a homogeneous tool because it combines the toughness of the tool holder with the hardness of the insert.
Inserts are usually indexable, meaning that they can be exchanged, and often also rotated or flipped, without disturbing the overall geometry of the tool. This saves time during machining operations by allowing fresh cutting edges to be presented periodically without the need for sharpening, setup changes, or entering new values into a CNC program.
Manufacturing inserts is a high-precision process. Exact geometry and a perfect surface finish are critical. Even minimal deviations can adversely affect the service life and performance of the insert. Defects that are invisible to the human eye can cause immense damage. Careful quality control is essential to ensure that only flawless inserts leave the production process.
This was the challenge presented recently to engineers at Xactools, a manufacturer of automated inspection and measurement systems in Bönnigheim, Germany. Xactools needed to design and build a flexible, high-speed automated inspection system for a Scandinavian manufacturer of indexable inserts.
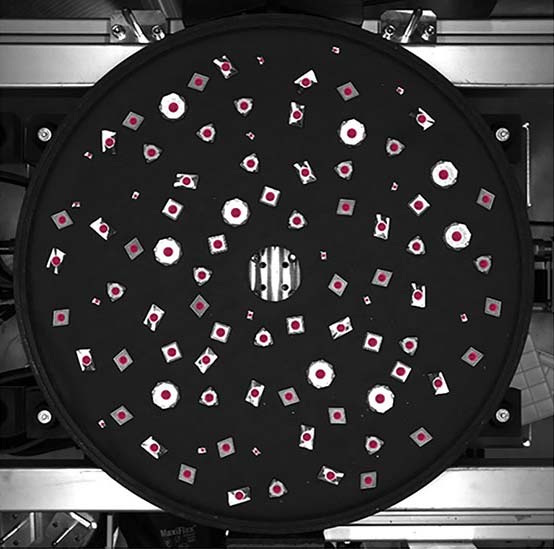
The AI vision software had to be trained to recognize the numerous color deviations of the surfaces of the parts. Photo courtesy IDS Imaging Development Systems
Some 1.2 million inserts leave the Scandinavian company’s production hall every week. The inserts are manufactured using the sintering process, in which powdered metals, hard metals and other materials are pressed into the desired shape and then bonded together under heat and pressure. The strong and robust structure created in this way makes it possible to combine materials with different properties to achieve particular cutting and wear resistance properties. After the sintering process, the edges of the inserts are rounded and ground, and their surfaces are blasted, ground and coated.
A machine vision system is used to inspect the inserts immediately after sintering. “The earlier that defects are detected in the process, the better and cheaper it is to rectify them,” says Marvin Krebs, director of technical sales at Xactools.
The automated system consists of eight high-resolution cameras, two delta robots, and a rotary indexing table. IDS Imaging Development Systems provided the cameras, the image-processing computers and DENKnet artificial intelligence inspection software.
Flexibility was a major challenge for the project. Inserts come in myriad shapes, sizes and materials to match specific cutting and shaping applications. The insert manufacturer offers some 2,800 inserts in its portfolio, which can be divided into almost 100 geometry families. Xactools needed to automate handling and inspection for all of them.
Engineers also had to cope with natural variation within a specific batch of parts. “Another challenge results from the numerous color variations created by the powder pressing process,” explains Krebs. “If certain parameters, such as time, pressure or positioning vary, this leads to color or gloss level deviations or to a different distribution of speckles on the surface. However, these are not defects.”
The AI-based image evaluation software had to be trained to recognize the numerous possible color deviations of the surfaces and rate them as “OK.” On the other hand, the smallest irregularities, such as cracks, scratches, inclusions or other anomalies, must be recognized as such and classified as “not OK.”
Inspecting metal surfaces has always been challenging, since they can be matte, shiny or even reflective. “The AI had to be extremely trained to variations and lighting conditions for this application,” emphasizes Krebs.
In addition to visual appearance, the vision system had to check the geometry of the inserts. Shapes such as triangle, rectangle, rhombus or square can be found in countless variations and are therefore divided into manageable subcategories, so-called geometry families. Engineers at Xactools pre-selected shapes to train the AI initially. Then, almost 100 geometry families were defined and taught by the insert manufacturer. What sounds like a laborious undertaking was done surprisingly quickly.
“No more than 20 to 30 images were needed to teach each geometry family,” recalls Krebs.
The AI was integrated into the production line in just a few months and achieved almost perfectly reliable results right from the start.
“Indexable inserts identified as defective are sorted out and grouped according to the size and position of the defect. The AI image analysis detects more than 99 percent of production errors,” adds Daniel Routschka, sales manager for artificial intelligence at IDS.
How It Works
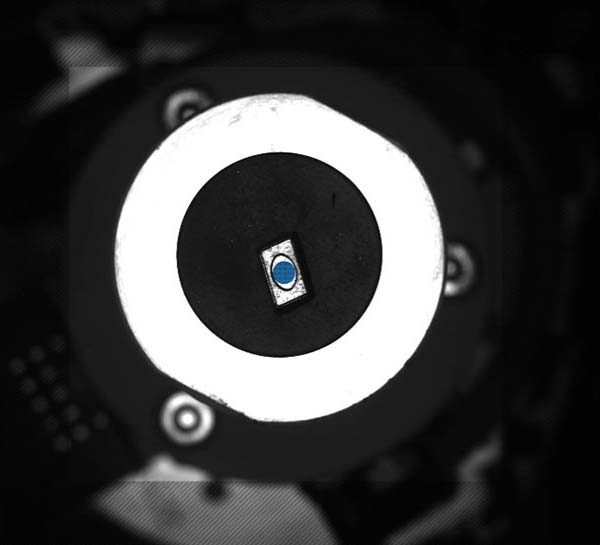
The vision system can see exactly where and in which rotational position an insert is positioned, so a gripper can place it over a pin in a pallet. Photo courtesy IDS Imaging Development Systems
Eight cameras with resolutions between 5 and 30 megapixels provide live images of the inserts, which are positioned by magnetic or interchangeable grippers. For example, a camera records the individual inserts from below and from above to check them for surface defects. Two other cameras check their cutting edges. A lighting screen measuring 1 meter by 1 meter provides high illumination at the inspection stations.
“The system detects defects in the thousandth of a millimeter range,” emphasizes Krebs. “This ensures that no damage is caused to the high-end surfaces to be processed later.”
The system also records images of the contour and position of the panels after inspecting the surfaces and edges. It can see exactly where and in which rotational position the insert is positioned, so the magnetic gripper can place it over a pin in a pallet. To ensure this, the gripper moves the insert over a camera that detects the exact position of the hole from below. At the same time, the contour of the insert and the outer edge of the gripper are detected to correct the position of the insert. In addition, each individual pin position is detected to recognize bent and broken pins so that they are not palletized in the first place.
“The system has been running for six months and the self-learning AI now recognizes parts that it has never seen before,” says Krebs. “After just three to four months, new versions of inserts no longer had to be trained for inspection. The underlying geometry is no longer relevant for the AI; it knows the contour and can also differentiate between ‘OK’ and ‘not OK’ for new parts.”
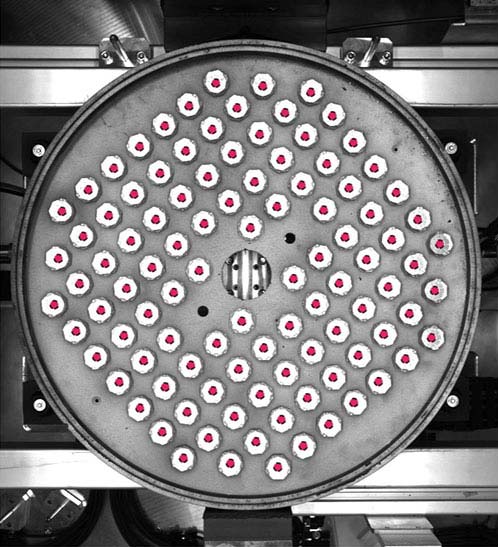
AI recognizes holes in the inserts, enabling them to be picked and placed by a delta robot. Photo courtesy IDS Imaging Development Systems
For Krebs, the added value of the DENKnet system compared to conventional image processing is obvious: “Without AI, the creation of part families and defect detection would be completely unthinkable,” he says. “With rule-based image processing, the robot would also recognize parts within the standard range as ‘not OK’ and sort them out.”
In addition, no hard coding is necessary, and the AI software can work with a variety of networks. “We were able to easily embed the DENKnet AI and several object classes for defects into our own image processing software via an API,” says Krebs.
The performance of the system is almost unique. The entire inspection process takes place in a cycle time of 4 seconds, with almost 100 percent picking efficiency. The image analysis of live images from eight cameras via a Dynamic Link Library requires enormous computing power.
“We work with DENKnet for a good reason. The performance is not comparable with that of other providers; it is truly excellent,” emphasizes Krebs. “Using artificial intelligence in the most diverse variants on this scale has never been done before.”
If IDS’ AI vision software can handle the varied surfaces and geometries of cutting inserts, as well as tolerances in the thousandths of a millimeter range, it can work with many other demanding applications, predicts Krebs. The system can be operated without programming knowledge and enables the automated training of AI with just a few clicks.
“This system can be customized to any use case and there are no limits—no matter how many part classes, which camera technology is used, how large or small the images, or even how mixed the data sets are in terms of resolution and type,” adds Routschka.
“Over 95 percent of our measuring and testing systems have at least one AI object class integrated. The potential areas of application are getting bigger and bigger for us, the market is growing,” confirms Krebs.
For more information on vision systems, read these articles:
Vision System IDs Part Codes Superfast
New Tech for Sensors and Vision
Beyond the Human Eye: AI Improves Inspection in Manufacturing