Clinching is a high-speed, mechanical fastening technique for joining sheet metal. This inexpensive and easily automated process requires a press, a punch and a die. The punch pushes the sheet metal into a die, forming a mechanical interlock.
Clinching is ideal for joining sheet metal for several reasons. First, clinching requires no fasteners. Therefore, the cost of the fasteners and equipment to feed them is eliminated. And, clinching can join sheets of different thicknesses or materials. The process can even be used on stainless steel. Clinching will not damage anticorrosive coatings, and an adhesive or other material can be located between the sheets.
Clinching is mainly used to assemble white goods, heating and ventilating components, and automotive parts. These industries routinely use precoated, enameled and galvanized materials. Spot welding can destroy the protective coatings on these materials. Also, clinching requires none of the peripheral equipment needed for spot welding, such as high-current electrical and cooling systems, and ventilation equipment.

Clinching offers many advantages over spot welding and riveting. Photo courtesy Kistler
One of the leading suppliers of clinching technology is BTM Co. of Marysville, MI. In 1966, engineers Milus Allison and Edwin Sawdon started BTM by creating highly specialized stretch bending machines for producing structural metal components and decorative sheet metal trim parts. Recognizing a need for an inexpensive, compact, high-force assembly press, the two men invented a pneumatic toggle press, which became the first of many BTM patented products. As sales grew, the company explored new applications for their versatile press and in 1980 invented the sealed clinch joint, Tog-L-Loc.
Today, BTM remains in Michigan, but also has operations in Germany, Sweden, England, Mexico, China and Brazil. The Swedish operation, BTM Scandinavia AB, was established in Kalmar, Sweden, in 1990. It employs seven people and services and services customers in a variety of industries.
“Clinching offers many advantages over spot welding and riveting. With our various clinching technologies, we can offer an optimum solution for almost all applications in sheet metal joining,” says Bo Claesson, one of the directors of BTM Scandinavia. “In contrast to welding, there is no heat input on the parts, so material structure and properties remain constant. In addition, clinching does not leave residues on the parts, nor does it require additional fasteners, which saves weight.”
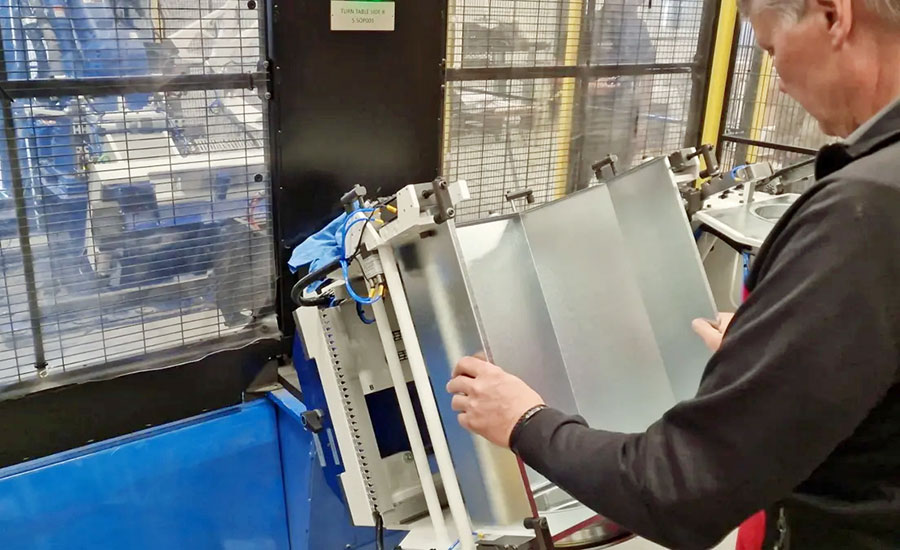
An assembler loads sheet metal parts onto a rotary indexing dial. Photo courtesy Kistler
Clinching With a Robot
Recently, BTM Scandinavia was contacted by contract manufacturer Steinadler AB of Astorp, Sweden, for help producing a ventilation housing that had previously been assembled with spot welding and blind rivets. The task was to join six metal sheets of different thicknesses with 34 clinch joints. The manufacturer wanted an energy-efficient process and durable, residue-free joints.
BTM Scandinavia replaced the spot-welding process with a semiautomatic clinching process featuring a six-axis robot and an energy-efficient electromechanical press from Kistler.
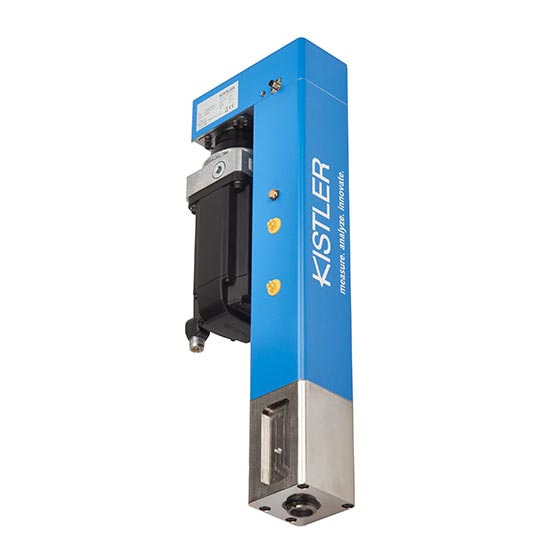
Quality assurance is supplied by the maXYmos system. It controls, visualizes and monitors the clinching process and makes production data accessible for higher-level software systems. Photo courtesy Kistler
“Dragiza Tosovic, the CEO of Steinadler, explicitly asked for the newest and best technology for production of the ventilation housings. We had to consider both economic and ecologic aspects. So, it was a perfect opportunity for the new NCFC servo press from Kistler. With its low weight of 46 kilograms, compact size, and maXYmos process monitoring system, it is ideal for robotic assembly,” reports Claesson.
The robotic work cell uses a rotary indexer position the parts. The robot is equipped with C-frame tooling and a NCFC servo press that applies 55 kilonewtons of force. Integrated sensors on the press measure force and displacement during clinching. Quality assurance is supplied by the maXYmos system. It controls, visualizes and monitors the clinching process and makes production data accessible for higher-level software systems.
“The main challenge in this application was to realize 34 clinch joints in a cycle time of one minute and 20 seconds,” explains Volker Eilmannsberger, development engineer for joining systems at Kistler. “In addition, the assembly had to be moved multiple times to reach all the clinching positions. This parallel operation also has an influence on cycle time. Thanks to the NC functionality of our joining system, the different traverse paths could be optimized relatively simply.”
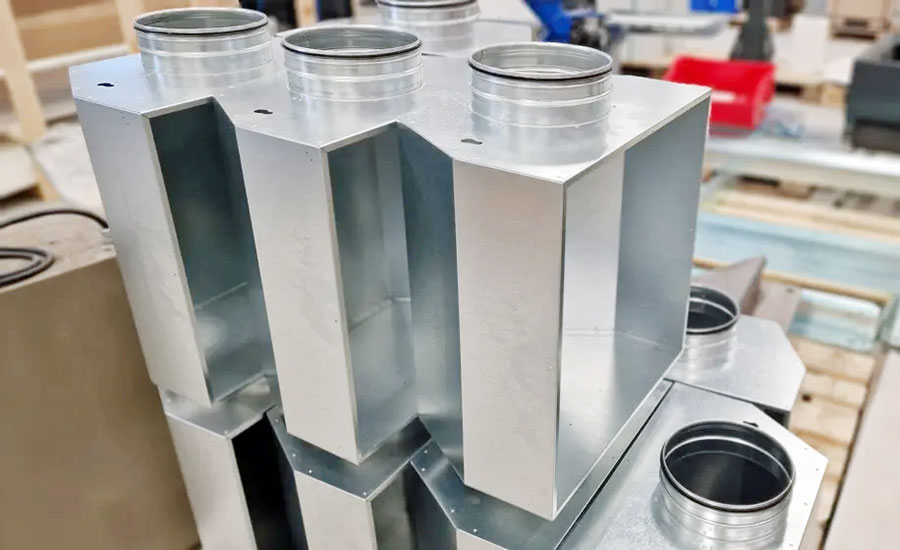
The main challenge in this application was to produce 34 clinch joints in a cycle time of one minute and 20 seconds. Photo courtesy Kistler
Thanks to its small size and low weight, the NCFC press is particularly suited for robotic assembly. Efficient integration is fostered by the new hybrid cable technology of the press. Energy, signals and data are transmitted via a single hybrid cable.
The work cell has worked so well that another production cell for ventilation housings is already in progress.
For more information on presses, read these articles:
Swiss Engineers Develop Electric Airplanes
Servo Presses Save Energy and Improve Quality
Servo Presses Ensure Quality of EV Axles