Gaskets have been around for decades. They provide a reliable, cost-effective mechanical seal that fills the space between two components or flanges with flat surfaces.
Gaskets are used to prevent leakage of liquids, gases or debris into or out of joined parts. The devices are widely used in a variety of industries, including appliance, automotive, consumer electronics and medical device manufacturing. They’re found in everything from agricultural equipment to washing machines.
Many gaskets are made out of a deformable material that creates a static seal, even if the relatively flat flanges have surface irregularities. A liquid gasket is dispensed onto a substrate to provide 100 percent contact between mating plastic, metal or wood surfaces. The gasket provides a seal that prevents leaking, keeps out dust and moisture, dampens vibration and shields against electromagnetic interference.
“Sealing with gaskets is usually done either via compression or molded gaskets like O-rings, and requires more component design knowledge compared to other sealing applications or technologies,” says Martin Kluke, senior product manager for radical-curing formulations at DELO Industrial Adhesives.
“Especially for compression sealing, knowing the dimensions of each part, such as depth, width and gap size, and the pressure created after assembly, is important,” explains Kluke. “Surface roughness also plays a role in creating a tight seal.
“If the application has a simple round geometry, a rubber O-ring will be the typical gasket,” notes Kluke. “However, if it has a complex shape or geometry, liquid sealants [are] ideal, as they can be easily adapted to any geometry.
“Another advantage compared to solid sealants is that liquid sealants rest on more than just the rough, raised areas of a component’s surface,” Kluke points out. “They therefore seal rippled surfaces better and compensate for larger production tolerances.”
Most manufacturers have replaced traditional die-cut or molded solid gaskets with form-in-place and cure-in-place liquid gaskets.
With form-in-place (FIP) gaskets, sealant is applied directly to the joint between the connecting components and forms the seal there. The sealant then cures once assembled or during the assembly process, allowing it to conform exactly to the space between components and achieve an effective seal.
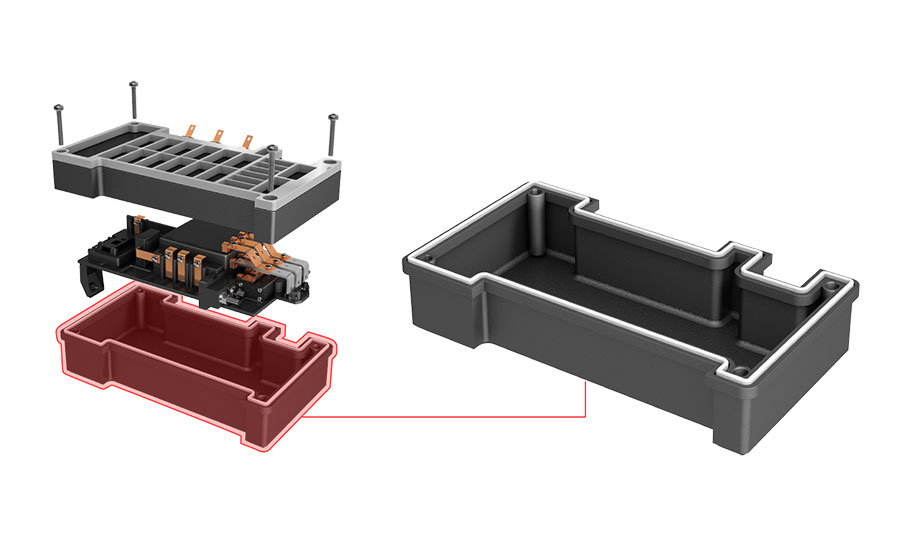
New types of form-in-place gaskets are being developed to address growing demand for highly reliable automotive electronic components. Illustration courtesy Henkel Corp.
However, with a cure-in-place (CIP) gasket, sealant is applied to a component and then cured before its assembly with its corresponding part. Curing of the sealant takes place on the spot where it was applied, not between the joining surfaces of the components needing to be sealed.
“CIP means that the sealant cures so quickly in the manufacturing process that it can be immediately assembled and compressed,” says Kluke. “Once this is complete, the entire assembly group can be moved down the line for the next process steps.
“While slower, room-temperature curing products typically use the FIG process," explains Kluke. "High-speed products like UV- or light-curing acrylates allow for the CIP process and its high production volumes.
“Another thing that [engineers] should consider is the production environment,” notes Kluke. “For example, in the automotive industry, [many parts and subassemblies must be] 100 percent free of silicones and other substances that may compromise paint wetting, as this could subsequently affect adjacent production processes. This is not the case with light-curing acrylates.”
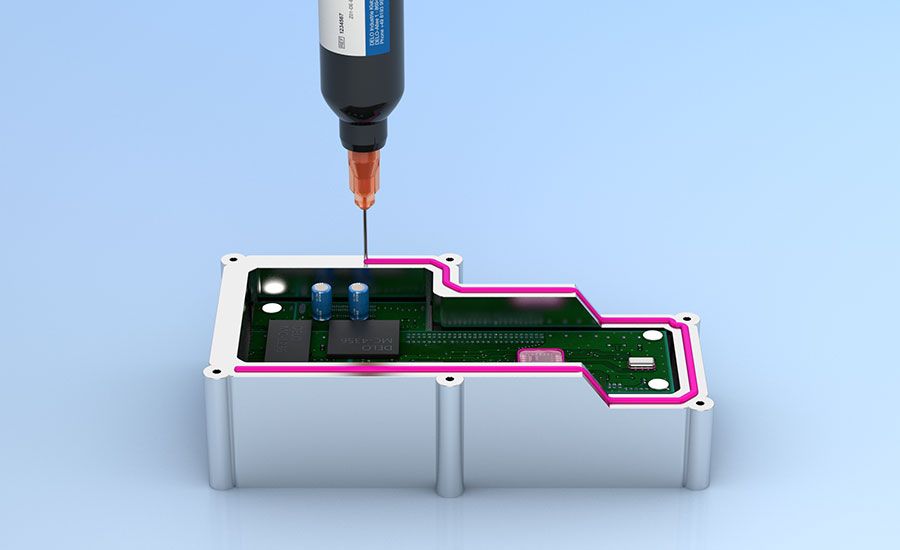
Most manufacturers have replaced traditional die-cut or molded solid gaskets with form-in-place and cure-in-place liquid gaskets. Photo courtesy DELO Industrial Adhesives
Numerous Applications
Traditionally, some of the most common uses for gasket sealing have been in the automotive and electronics industries. Automotive applications include ADAS components, battery disconnect units, door handles, electronic control units, engine covers, gear components, oil pans and pumps. Electronic applications include sealing housings, junction boxes and modules, and assembling loudspeakers.
“Demand for gasketing is growing—especially for UV-based technology—due to increasing use of electronics in many types of products,” says Harry Arnon, president of Hernon Manufacturing Inc. “A lot of military and defense applications use it to encapsulate sensitive components.
“Engineers are looking for turnkey solutions that dispense sealant, cure it and then visually inspect it,” claims Arnon. “Benefits include less handling, fewer operators and less space, ultimately resulting in higher throughput and fewer rejects. Everyone wants high speed, consistency and repeatability.”
“Gasketing really hasn’t changed much in the last 20 or 30 years,” adds Tom Muccino, zone sales manager at Nordson EFD. “But, there are a lot more products that contain electronics today, which is driving demand.
“Liquid gasketing typically involves dispensing a bead around the outside diameter of a component,” says Muccino. “Some applications require complex geometries, but for the most part, it’s relatively basic and simple compared to other things that we deal with.
“Automotive applications certainly remain hot, but any type of electronic or electrical enclosure typically uses gaskets,” explains Muccino. “One of the trends we’re seeing is a continued push to much smaller packaging sizes.”
Cutting-edge gasketing applications, such as electric vehicle batteries and fuel cells, are creating new demand for liquid sealants today.
“The up-and-coming new mobility market has led to special requirements for gasket technology, such as sealing against special aggressive media,” says Kluke. "Applications include protecting components against water-glycol mixtures used as a coolant in EVs and sealing hydrogen fuel cells to prevent diffusion.
“Multifunctionality is another trend, with special properties like EMI-shielding functionality, thermal or electrical conductivity, or flame retardancy having been specially requested by customers,” Kluke points out.
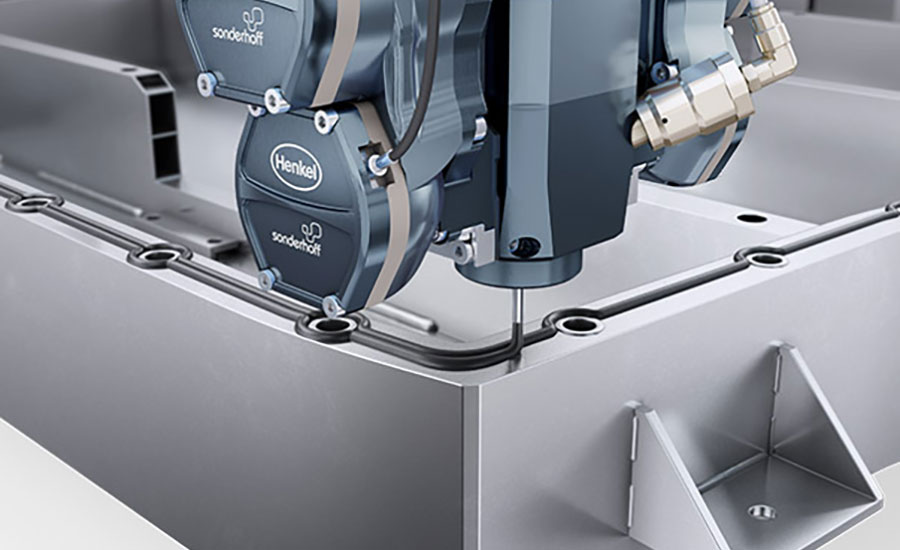
Form-in-place gaskets are used to seal a wide variety of auto parts. Photo courtesy Henkel Corp.
“Products on a silicone or polyurethane base have often been used for liquid gaskets,” notes Kluke. “However, these two-component systems cure slowly and are therefore better suited for large individual components or small series. In the case of large series, the albeit uncomplicated and flexible process using liquid gaskets has often not been able to compensate for its lower curing speed compared to rubber or TPU seals.
“Light-curing one-component acrylates that have been on the market for some time…leverage their strengths in high-volume series,” says Kluke. “High-energy UV light ensures that the adhesive reaches its final strength within a few seconds, thus allowing short cycle times and direct processing of the components, which are important to achieve a high production volume.
“Unlike slow-curing silicone or polyurethane-based liquid sealants, light-curing liquid sealants enable high-speed production processes that can be fully automated, enabling the CIP process,” claims Kluke.
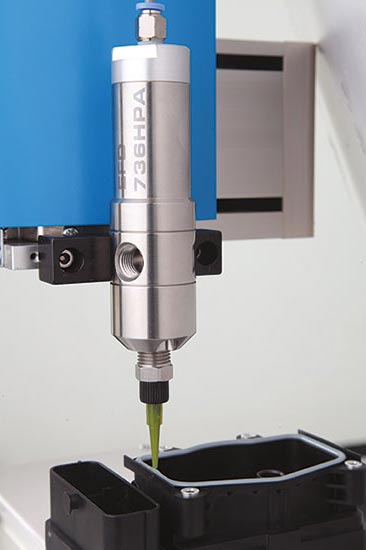
Liquid gasketing typically involves dispensing a bead around the outside diameter of a component. Photo courtesy Nordson EFD
What’s New
Engineers have a variety of products available for gasket sealing applications, including both new materials and dispensing equipment.
Hernon’s UV FOG (Form On Gasket) is an ultraviolet sealant that creates a soft, flexible gasket in any size or shape. “The resin can be used as form-in-place gaskets in oil and coolant systems,” says Arnon. “Typical applications include engine covers, oil pans and other fluid seal systems.”
UV FOG 702 is a popular electron beam and ultraviolet-curable product that provides excellent adhesion to shaft seals and oil seals. It cures within seconds of exposure to UV light and has excellent adhesion to a variety of materials, including ceramics, glass, metal and plastic.
“Because the sealant is a 100 percent solid system, there’s no shrinkage due to solvent evaporation,” claims Arnon. “It cures in about 4 seconds.
“Compared to older generation alternatives, it’s a significant improvement,” notes Arnon. “In the past, solvent could take up to 8 hours to cure at room temperature. With UV technology, you apply it, you zap it and you’re done.”
DELO recently unveiled a new light-curing CIP product called Photobond SL4166. It is especially effective at sealing from aggressive media like hot oil.
“[The sealant] maintains a certain recovery effect, even after storage at 160 C in hot oil, and could replace slow humidity-curing silicones, instead curing within seconds,” claims Kluke. “It is ideal for use in the automotive industry for sealing oil pans, engine covers and transmission housings, [but can also be used to assemble] electronic or power control units.
“With a compression set of 7 percent, Photobond SL4166 has good elastic recovery, with the highly flexible material springing back quickly after being compressed,” says Kluke. “These properties ensure a reliable seal and help manufacturers meet their sealing requirements.
“The one-component sealant is free of paint-wetting impairment substances,” adds Kluke. “This solvent-free, flow-resistant, highly viscous sealant cures via UV or visible light in a matter of seconds without thermal influence, enabling the CIP process.”
To address growing demand for highly reliable automotive electronic components, Henkel Corp. recently developed Loctite SI 5972FC. It significantly reduces cycle time by providing a robust assembly seal capable of passing leak tests without prolonged cure time. By avoiding the need for curing ovens, the material also helps manufacturers reduce energy usage and carbon emissions.
“The revolutions in electrification and autonomy are creating an exponentially growing demand for highly reliable automotive electronic components, and a need to optimize every aspect of component design and manufacture,” says Arthur Ackerman, business development manager for automotive electronics at Henkel. “[Our] innovative solution for silicone liquid gasketing [is designed] for the next generation of automotive electronic components.
“Loctite SI 5972FC is a one-part, room-temperature vulcanizing (RTV) silicone FIP gasket that accelerates the process of electronic module sealing,” claims Ackerman. “With adhesion to a range of metal and plastic surfaces, the highly dispensable liquid material has been specifically designed to pass OEM’s leak or blow-out pressure tests immediately after assembly, minimizing the need for time- and space-intensive staging.
“Module sealing is an essential final stage in the assembly process,” explains Ackerman. “While liquid silicone gasketing solutions have proved a versatile option that can address multiple configurations without the inventory challenges and manual assembly required by traditional rubber O-rings, the RTV curing process can be time consuming.
“To meet stringent OEM pressure testing, post assembly staging to achieve a full cure can take several days,” Ackerman points out. “This not only prolongs cycle times, but also consumes precious floor space in the manufacturing environment.
“Loctite SI 5972FC changes all this,” notes Ackerman. “Thanks to its unique design, it can pass a 3-psi leak test immediately after assembly. Even higher leak test pressures can also be passed in relatively short periods. In addition, the material’s noncorrosive outgassing and low volatility makes it ideal for sensitive electronic components.”
More Efficient Dispensing
When dispensing liquid sealant, it’s important to apply the material precisely along the contour of the part. However, on complex components with various corners, radiuses and surfaces, consistent, gap-free dispensing can be challenging.
To address this issue, Scheugenpflug GmbH recently developed the DC803 Dispensing Cell. It is designed to make the gasket dispensing process faster, easier and more reliable.
Software enables dispensing speed to be adapted to the gantry speed. Since the gantry can accelerate on straight sections, dispensing speed is automatically increased at the same time. “Similarly, the gantry slows down along tight radiuses, so dispensing is adjusted to prevent material from accumulating,” says Sebastian Schmitt, area sales manager at Scheugenpflug. “The process time can be significantly reduced as a result of this direct link. In some applications, it is reduced by up to 50 percent.
To ensure optimum and traceable quality, vision systems are used to check the width, position and uninterrupted application of the sealant during application. There is no need for a separate inspection station, which saves money and cycle time.
Vision sensors are mounted directly on the dispensing head above the nozzle. Inspection is performed in real time as the sealant is applied, so plant personnel know immediately whether a part is good or not good.
“Inspection with RTVision is available with 2D or 3D sensors,” explains Schmitt. “The 2D sensor uses an LED light source to detect the width and continuity of the application by contrasting the bead with the background. The 3D sensor uses six lasers as the light source to evaluate the third dimension, height, as well.”
User-friendly software lets engineers easily enter the parameters for good parts and bad ones. Detailed visualization means that the status is instantly visible.
Jetting systems are commonly used to dispense liquid sealant for gasketing applications. Earlier this year, Nordson EFD unveiled PICO Nexμs, which connects dispensers to Industry 4.0 technology. It enables engineers to connect, control and monitor jetting functions using Industrial Ethernet protocols from a human-machine interface (HMI) of their choice at the point of dispense.
“For most automated production machines, standard jetting controllers are panel-mounted away from the point of dispense, making adjustment and monitoring of the dispensing parameters inconvenient to the user,” says Claude Bergeron, PICO product line manager at Nordson EFD. “[Our new] jetting controller eliminates this hassle.
“Its compact, 24V DIN-rail construction makes it easy to mount inside an existing machine cabinet, saving valuable space near the automated machine,” claims Bergeron. “It is especially well suited in multi-valve installations where machine real estate is limited.”
PICO Nexμs controllers use standard Industrial Ethernet protocols such as Profinet and EtherNet/IP to communicate with PLCs or other plant controllers. This allows engineers to control multiple jetting systems through a HMI at the point of dispense. An intuitive web interface also simplifies setup, programming and monitoring.
“PICO Nexμs…connects to factory automation,” explains Bergeron. “It connects to the jetting process controls. It connects to the machine. And, it connects the machine operator via HMI for real-time manufacturing information, enabling a data-driven production process and greater production yields and efficiencies.”
ASSEMBLY ONLINE
For more information on adhesives and dispensing systems, read these articles:
Gasket Design Rules
Process Control for Dispensing Gaskets
Troubleshooting the Dispensing Process