As of December 2023, China had the largest stock of plug-in electric passenger cars with 20.4 million units, almost half of the global fleet in use. China also dominates in deployment of plug-in light commercial vehicles and electric buses. In 2019, more than 500,000 electric buses and almost 250,000 electric light commercial vehicles were operating in the country. That’s 98 percent of the global stock of electric buses and 65 percent of the global fleet of electric commercial vehicles.
One of the newest EV OEMs in China is Hycan Automotive Technology Co. Ltd. Headquartered in Guangzhou, China, the company was formed in April 2018 as a joint venture between GAC Group (the fifth largest automobile manufacturer in China) and Chinese EV startups GAC Aion and Nio Inc.
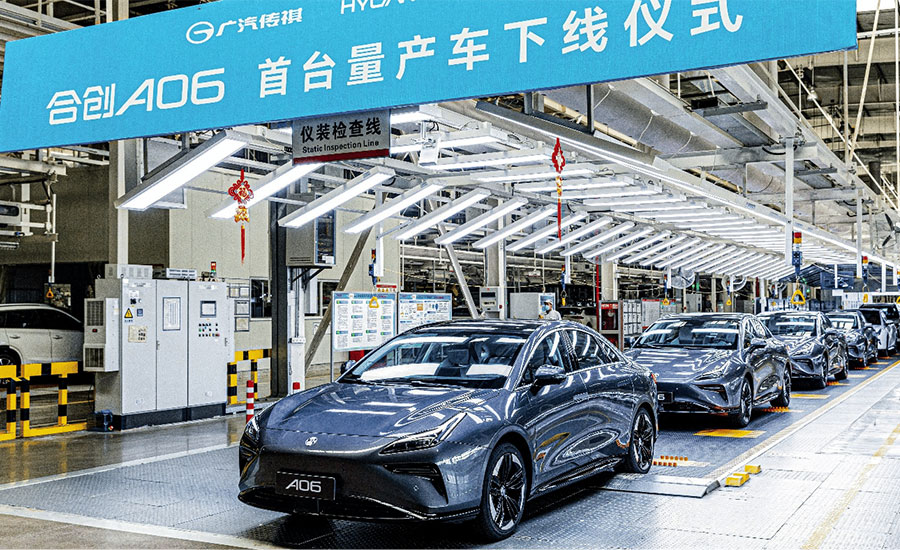
Hycan’s sales have increased from 659 vehicles in 2020 to 15,980 in 2023. Photo courtesy Hycan Automotive Technology Co. Ltd.
The new company has done well. Hycan’s sales have increased from 659 vehicles in 2020 to 15,980 in 2023.
The company offers four models: the Hycan 007, a midsize electric SUV; the Hycan Z03, a subcompact electric crossover SUV; the Hycan A06, a midsize electric sedan; and the Hycan V09, an electric multipassenger vehicle.
The company has placed a strategic focus on attracting young generations in the Chinese market. For example, Hycan vehicles feature a digital smart assistant, named “Little Can,” that can pull up the car’s navigation, control the music, adjust the cabin temperature, open or close windows, and take a photograph of passengers in the cabin.
Flexible Automation
Hycan operates two assembly plants in China—one in Hangzhou, on the central coast, and another 800 miles southwest in Guangzhou—each with a capacity to produce 10,000 vehicles annually. Both plants are capable of producing multiple models on the same line.
Flexible automation is critical to the company’s goal of offering a rich product range in a short period of time. Robotics and automation company Comau is helping Hycan meet that goal.
Specifically, Comau designed and built an intelligent and flexible automated framing line for Hycan’s Hangzhou assembly plant. The automated system can randomly switch between producing any of the company’s four models. It is currently mass-producing Hycan’s A06 sedan and Z03 SUV at rate of 60 units per hour.
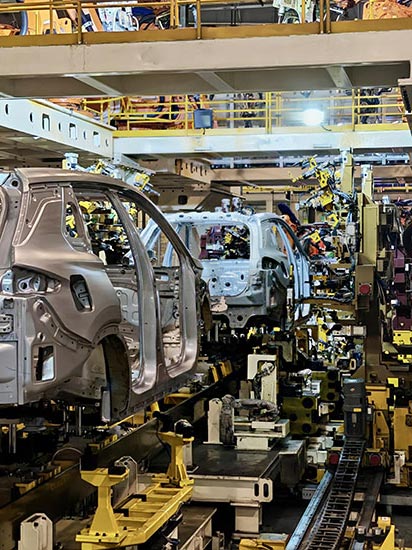
Comau designed and built an intelligent and flexible automated framing line for Hycan’s Hangzhou assembly plant. Photo courtesy Hycan Automotive Technology Co. Ltd.
The line is based on Comau’s modular, flexible and expandable Open RoboGate framing system. Customizable work-holding “gates” are the heart of the system. The gates are equipped with clamps and fixtures to hold the body parts in place for welding. The gates work in pairs—one on each side of the vehicle body. Each pair is designed for a specific vehicle model.
While one model is being produced, gates for other models are stored nearby. When a different model is next in the sequence, the previous gates automatically move out and the gates for that model move in. Up to six gates can be stored on each side of the line (for a total of 12 gates), and the gates can be deployed in any sequence.
The frame parts are designed to fit together with toy tabs, so each body enters the welding station preassembled. When the body enters the station, the transfer system lowers it onto fixed supports, and servo clamps deploy to hold the body in place. Then, the gates move in from each side of the vehicle, providing up to 50 kilonewtons of holding force on the parts.
With the body secured, up to 18 six-axis robots surround the body performing spot welds. The robots are located above, to the side, and below the body. With so many robots working simultaneously, more than 100 spot welds can be accomplished in just a few seconds.
When the welds are finished, the robots move out of the way, the clamps release, the gates slide back, and the transfer system raises the body and moves it to the next station.
Comau’s NJ4 six-axis robots handle the welding. Equipped with hollow wrists, the robots are designed for high-density welding applications. Programming done via off-line simulation is 100 percent accurate on the line. Cables and hoses for clamps and welders are enclosed and shielded for maximum uptime. The welding guns are servo driven for flexibility, maximum uptime and energy efficiency.
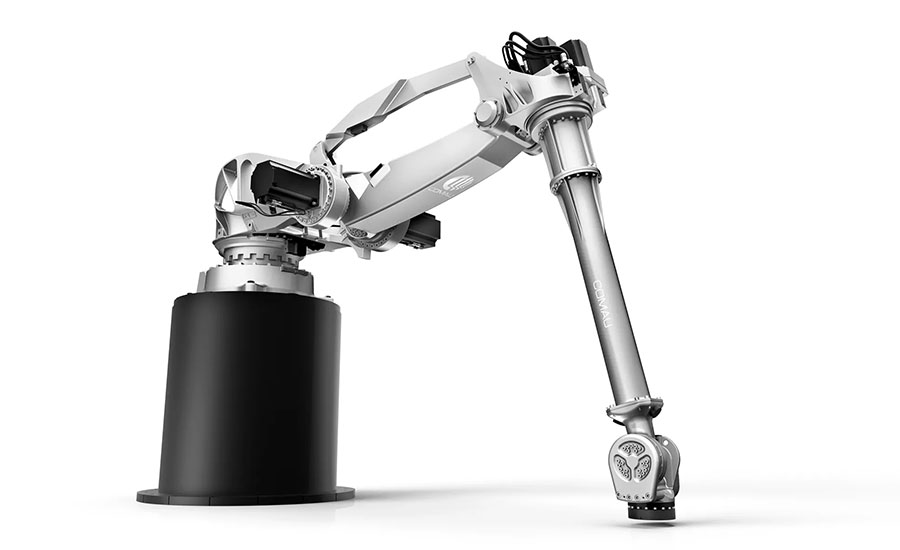
Comau’s NJ4 six-axis robots handle welding at Hycan. Equipped with hollow wrists, the robots are designed for high-density welding applications. Photo courtesy Comau
Comau added flexible servo positioning mechanisms to the conveying system to shorten the overall cycle time. The system has an overall equipment effectiveness exceeding 90 percent. And, because the system can produce up to six models at the same time, the line can run continuously without downtime for changeover.
“The results of the first collaboration between Hycan and Comau have been very satisfactory,” says Feng Yiqiang, director of Hycan’s intelligent manufacturing process. “Comau’s innovative technologies and professional engineering management throughout the project have fully demonstrated its position as a leader in body systems and provided an important guarantee of the processing efficiency and quality for our first model production project.”
For more information on automated assembly, read these articles:
Comau Robots Assemble Electric Version of Fiat 500
Comau Automates Production of Next-Generation EV Batteries
Smart Robot Automates Inspection of Helicopter Blades